by MAURA KELLER
Few words captivate the automotive recycling sector more than the word ‘change.’
Anyone with even a casual understanding of the auto recycling marketplace recognizes that change is constantly afoot. And for the past 50 years, many recycling companies, both small and large, have embraced technological innovations to stay ahead of the game.
Auto recycling has long conjured up images of the old “junkyard” — rows of rusty, dusty and dented vehicles sandwiched against one another, awaiting the crusher. For some recycling companies this image still rings true, but the remaining aspect of their recycling process includes a unique mix of factors like environmental reforms, the economy, the influx of international and technological advancements.
The evolution of the relationship between automakers and recycling industry partners is the result of the ongoing technological changes facing the auto industry. Due to the advancements made in the building of today’s automobiles, the auto recycling industry also needs technology advancements to properly dismantle, handle and recycle autos.
According to Automotive Recyclers Association, auto recycling companies are faced with the recycling of new technologies such as high voltage batteries. The automotive industry has published dismantling manuals for these batteries and is developing standards for labeling, transportation, testing, packaging and recycling through Society of Automotive Engineers workgroups.
As with the influx of high voltage batteries within automobile construction, plastics of all types are requiring changes in technology within the automotive recycling industry.
According to SPI: The Plastics Industry Trade Association, on average, plastics reduce the weight of automobiles by 500 to 750 lbs. But with about 39 different types of plastics being used in automobiles, recycling those vehicles at their practical end-of-life – about 27 million every year around the world – can be a challenge.
However, automotive plastics recycling is still in its relative infancy, given the fact that recycling some plastic and polymer composite components can be challenging in terms of costs, technologies required and the very properties of plastics. As SPI explained, the technologies required to properly recycle the variety of plastics found within an automobile are significantly more advanced over merely sending the vehicle to a shredder.
Separation technologies such as float-sink tanks, magnetic separation, eddy current separators and laser and color-sorting infrared systems are available and being used by some recyclers in handling post-consumer materials. These options can cost millions of dollars per facility and represent only one part of the recycling process.
Because of the complexities involved in plastic recycling within the auto recycling industry, the Institute of Scrap Recycling Industries (ISRI) worked with recyclers to develop scrap specifications for plastic automotive bumper covers. The specifications for end-of-life vehicle bumpers help spur additional recycling and usage of the material.
In addition to the myriad of plastics currently found within today’s automobiles, some car manufacturers are exploring using new materials that will further require recycling companies to invest in the proper technology and training to handle these materials. For instance, bioplastics are now a part of the automotive manufacturing process. Ford is using soy to develop bio-based polyurethane foams on the seat cushions, seatbacks and headliners on various vehicle models. The company is also working with H.J. Heinz Company on research to use tomato fibers (skins, stems and seeds) for vehicle wiring brackets and storage bins such as coin and cup holders.
Toyota also is working to utilize plant-derived ecological plastic in some components of Toyota vehicles. The company’s commitment to bioplastic technologies is part of the company’s effort to replace 20 percent of a vehicle’s plastics with recycled or ecological plastic materials.
The use of bioplastics in vehicles is still in its infancy as these sustainable materials need to meet vehicle specifications and integrity standards and need to offer the same durability and performance of traditional plastics.
Technology Training
Technological advancements within the auto recycling industry are also dictating the demand for ongoing training on the part of recycling professionals. Recycling business owners continue to realize training is the key to getting the most out of their technology investment. In fact, many companies use training to keep their staff apprised of the latest technology so they can deliver technology-driven solutions to today’s auto recycling industry.
“Technology plays a key role in addition to training,” said Greta Houlahan, project manager, automotive certification at NSF International. “Independent, third-party certification ensures a recycler’s ability to meet criteria for grading, labeling and traceability in addition to vehicle acquisition, dismantling, inventory, training, customer service and auditing requirements.” More specifically, NSF International certification requires automotive recyclers to have continuous training in place and that the work be performed by trained and qualified individuals. For example, employees conducting dismantling shall be trained in safety related procedures.
Insurers and regulators want recycled parts that are graded and labeled properly. As Houlahan explained, with NSF International certification, recyclers can differentiate themselves in terms of meeting cycle time and ensuring accuracy when it comes to inventory, grading and part labeling.
“Annual audits, a key certification requirement, support ongoing compliance and emphasize continual improvement,” Houlahan said.
Technology will continue to impact the recycling industry and training will continue to be a key element in not only earning certification but also maintaining it. Houlahan pointed to the example of part complexity as an example of effective training.
As Houlahan explained, a recycler needs to know what to dismantle so sellable inventory is not crushed. An inventory management system to manage vehicles and parts is one solution.
“NSF International certification looks to ensure these systems are in place and that training occurs so that not only is the system used correctly, but that employees also know the critical role they play in operational efficiency, process improvement and safety,” Houlahan said. “Just as recyclers need to stay current on training and technology to be successful, certification organizations need to do the same.”
While vehicles are stocked with such advanced systems there will still be plenty of interchangeability of parts. The environmentally conscious generations will likely support the auto recycling industry’s green initiatives.
“The scrap metal market is still trying to fight its way back but the volatility there makes it tough,” Houlahan said. “The modern scrap recycling yard will need to shift its focus to the high end parts that contribute to new technology.”
Published in the April 2019 Edition
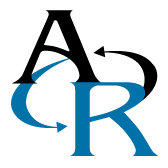