A groundbreaking ceremony in May marked the start of a project with major implications for Wieland – the foundry at the Vöhringen, Germany site will be expanded to include a recycling center. Thanks to state-of-the-art and efficient technology, this center will enable the processing of copper scrap, thus increasing the global recycling rate of Wieland products to more than 80 percent after commissioning.
“If we look at the foundry expansion in Vöhringen with a recycling center from a sustainability perspective, this is a global showcase project with a signal effect,” said Dr. Erwin Mayr, chief executive officer of the Wieland Group. “The new plant is an important building block on our way to sustainably closing the material cycle and increasing our global recycling rate to 100 percent in the near future.” This endeavor brings Wieland a big step closer to its goal of greenhouse gas-neutral production by 2045 at the latest. Other cornerstones of the decarbonization strategy are the electrification of all plants to phase out fossil fuels and the full use of renewable energy through green power supply contracts and in-house power generation using photovoltaic and wind power systems.
Vöhringen, a strategic base for Wieland, is crucial in terms of material supply. From here, plants throughout Europe and parts of Asia are supplied with high-quality semi-finished copper products. This investment is a commitment to the Vöhringen site, where 25 new jobs will be created, reinforcing confidence in the site’s potential.
In the future, the new plant on the Wieland foundry site will produce pure copper bolts with a recycled content of 100 percent. This innovative approach, using copper scrap and granulate as well as on-site production scrap, not only ensures the supply of material to various Wieland sites but also has a positive impact on the CO2 footprint of Wieland products. The recycling process, based on a highly energy-efficient method known as fire refining, sets new standards that benefit not only us but also our customers. They receive primary material with the lowest Product Carbon Footprint (PCF) in the industry, empowering them to make their own process chains lower-emission and more sustainable.
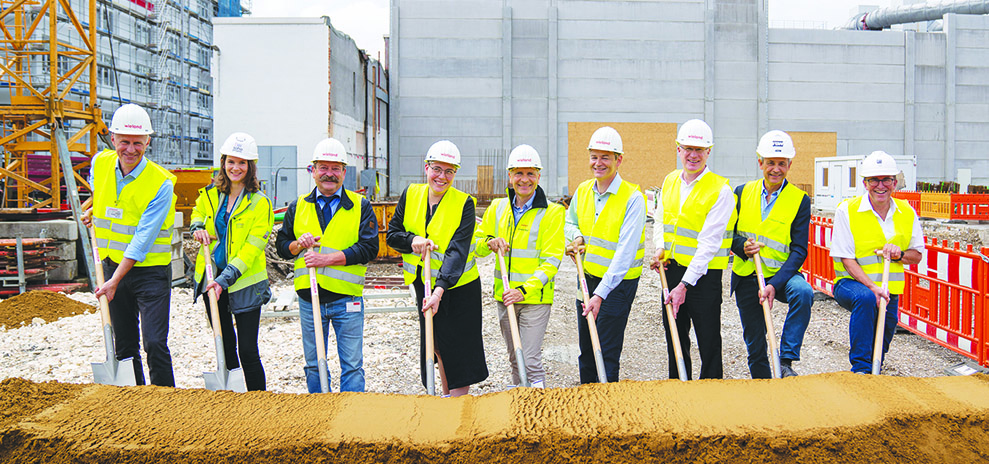
From left to right:
Rudolf Liebsch (director special projects, project manager Wieland Group), Lea Schmid (project manager soho-projekt GmbH), Herbert Walk (second mayor of Vöhringen), Eva Treu (district administrator of Neu-Ulm), Dr. Erwin Mayr (chief executive officer Wieland Group), Eckhart Zimmermann (vice president global engineering Wieland Group), Anton Zierhut (president Extruded Products Wieland Group), Rudi Mattes (head of sales and project management FBW Fertigbau Wochner), Reiner Fohler (chief construction manager Leonard Weiss GmbH & Co. KG).
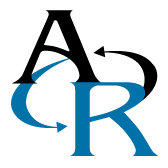