Plastic recycling technology has seen a tremendous shift in recent years, moving from mechanical recycling, which typically degrades plastic quality, to more advanced chemical recycling methods.
Co-founder of Denovia Labs, Nick Spina, said the company has been at the forefront of this shift, using proprietary depolymerization technology to revert plastics into their original chemical building blocks, regardless of contamination or complexity. This advancement allows the company to upcycle plastics into virgin-quality materials, increasing both the scope and efficiency of recycling efforts.
“In addition to this, AI-driven sorting systems and smart infrastructure are now playing a key role in automating and optimizing the recycling process,” Spina said.
One of the most groundbreaking advancements is Denovia’s depolymerization technology, which processes plastic waste in just five minutes – a dramatic improvement compared to older methods that take hours and hours. This speed significantly boosts the throughput of recycling facilities while lowering energy costs.
“Additionally, AI-powered vision systems and sorting technologies are rapidly enhancing the precision with which plastic materials are identified and segregated, allowing for higher purity and more efficient recycling streams,” Spina said. “Outside of Denovia, super-enzyme-based recycling has also emerged as a promising innovation, capable of breaking down PET plastic, but still has yet to prove itself.”
Michael Bockstaller, professor of materials science and engineering at Carnegie Mellon University, said that the technology surrounding plastic recycling is one of the most widely recognized ‘focus areas’ in the field of polymer science and technology.
“The concept of a ‘Circular Plastics Industry’ best describes the long term vision of current research,” Bockstaller said. A key challenge to accomplish a circular economy is recycling. Some examples of exciting new developments are:
- The application of machine learning methods to enhance the sorting and separation of plastic types and grades out of a waste product stream. This has the potential to significantly reduce costs and improve quality of recycled products.
- The advancement of catalytic methods to “depolymerize” plastics into their respective (low molecular) building blocks. This is important because established recycling methods result in a degradation of properties and hence the gradual decrease of performance of plastic products. The term “Depolymerization” refers to the “break-up” of polymers into small “monomer” materials from which new polymers can then be produced. Depolymerization has the potential to realize truly circular use of feedstock materials.
- The development of biological (e.g., bacteria) based approaches to degrade large volume plastics.
Rajesh Buch, senior global futures scientist, Global Futures Laboratory at Arizona State University, added that mechanical recycling of plastics involves shredding recyclable plastics (#1 PT, #2 HDPE and #5 PP) into flakes, using heat to reform into pellets and then using the pellets to inject mold products, press sheets, or extrude long pieces such as plastic lumber. Mechanical technologies have been around since plastics were widely produced and used in the 1950s.
“Thermal recycling is the burning of plastics to produce energy, since plastics are produced from crude oil,” Buch said. This technology is also referred to as pyrolysis, and can convert the plastics into gaseous fuel or liquid fuel (usually diesel fuel). Buch said the drawback of pyrolysis is that it produces toxic emissions (air and char) which have to be scrubbed at the exhaust or landfilled for the char.
“The other problem with pyrolysis is that it is not very effective in terms of extracting energetic value from plastic because the process is highly energy consuming – the net energy gain makes it less economically viable,” Buch said. “The newest technology being developed for plastic recycling is chemical recycling, which involves breaking plastics down into their component polymers and associated monomers, and then reforming the monomers back into polymers again. This technology has tremendous potential, but it is very capital intensive, and has yet to be proven as commercially viable.”
To take plastic recycling to the next level, Spina said advancements in the collection and sorting processes also are critical. This could involve scaling up the deployment of smart bins, which use sensors to sort and compact waste more effectively at the point of collection, and enhancing AI-driven systems to sort increasingly complex plastic materials.
“Additionally, further research into hybrid recycling methods – combining mechanical and chemical processes – could provide a more comprehensive solution for different types of plastics,” Spina said. “Collaborative efforts between municipalities, governments, and private industry to create standardized recycling systems are also needed to make recycling more seamless globally.”
Besides the technical aspects, for recycling to improve, Buch said the general public’s plastic waste diversion behavior has to be significantly increased (only about 9 percent of plastics are estimated to be recycled globally). To achieve that, Buch suggested that recycling services need to become widely available, recyclable waste protocols among municipalities need to become more consistent, and end markets for post-consumer recyclable (PCR) plastic need to become more widely available.
“Today, both mechanical recycling into pellets and converting pellets into product is limited nationally because these facilities are also capital intensive and require large volumes of materials to be processed to be profitable, which then requires acquiring that material from large geographic regions,” Buch said. “Finally, the commodity value of recycled pellets is almost the same as virgin pellets, which completely disincentivizes product manufacturers from adding PCR into the mix. This is changing, however, as more and more chief executive officers of finished product manufacturers are committing to making products with PCR.”
Challenges Aplenty
One of the biggest challenges is the complexity of the plastic waste stream itself. As Spina pointed out, plastics vary in composition and often contain additives that make recycling difficult.
“To address this, we need more standardized plastics and improved preprocessing technologies that can handle mixed or contaminated streams,” Spina said. “Public awareness and education also play a crucial role – encouraging consumers to dispose of waste correctly can help reduce contamination. Additionally, there is a need for greater infrastructure investment in recycling technologies to ensure scalability and accessibility across regions.”
Bockstaller said that many polymers are not used in “pure form” but as part of complex systems (e.g., food packaging). “One challenge remains the recycling of packaging films and substrates that often are constituted of layers of distinct polymer (as well as ceramic or metal) types,” Bockstaller said. “If the materials cannot be separated, this results in impurity formation in downstream products and reduces performance and usability of recycled products.”
Buch pointed out that existing solid waste management services in urban regions rely on improper community waste-diversion practices driven by inconsistent municipal waste protocols and policies, widespread waste collection networks serviced with fleets of GHG-intensive trucks, and large-scale, centralized, capital-and technology-intensive material recovery facility (MRF) operations.
“The outcome at the MRF creates additional challenges – from contamination by improperly cleaned or discarded materials, to improperly sorted materials, to limits on the types of plastics that MRFs can process, leading to inconsistent recyclable plastic feedstock for end markets,” Buch said. “Downstream of the MRF, the lack of guaranteed feedstock prevents investment and business attraction, and ultimately very few intermediate processors or end market producers are available in the state or in the region, and long-distance transportation becomes the only viable option to find the nearest end-markets, further exacerbating GHG emissions.”
As an additional result, Buch pointed out that these services are either inaccessible to rural communities in developed countries, or entirely unavailable in developing countries. In developed countries, smaller populations resulting in smaller volumes of materials and large distances to urban centers and associated end markets means rural communities dispose of these valuable materials in landfills. In developing countries, large informal communities of waste pickers are formed (70 percent of which are women) that rely on collecting and valorizing low-value commodities through volatile commodity markets to generate unsustainable daily incomes.
To counter all these systemic deficiencies of the existing plastic recycling industry, ASU’s Circular Plastics Microfactory is a groundbreaking initiative with the ambition to reshape global supply chains by creating a decentralized and distributed network of localized, circular microfactories.
“The microfactory model includes the entire lifecycle of plastic waste – collection, processing, conversion, and remanufacturing – creating a sustainable closed-loop system that catalyzes local economic development by creating jobs,” Buch said. “Unlike traditional recycling models that only handle parts of this lifecycle, ASU’s approach is fully integrated and localized, which allows for significant reductions in greenhouse gas emissions, economic inefficiencies, and the reliance on linear, waste-heavy supply chains.”
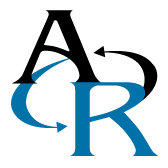