Manufacturer
American Baler American Pulverizer Bano Recycling s.r.l. BCA Industries Danieli Centro Recycling Eldan Recycling A/S Erdwich Zerkleinerungs-Systeme GmbH Forrec Recycling Franklin Miller, Inc. Granutech-Saturn Systems Hammermills International, LLC Harris Komar Industries, LLC Lindner Recyclingtech America Texas Shredder Lindemann Shred-Tech Sicon America SSI Shredding Systems, Inc. UNTHA Shredding Technology Inc. Weima America, Inc. Zato North America |
by MARY M. THORNTON
maryt@americanrecycler.com
The 2023 global car recycling market size was valued at $86.42 billion by Straits Research and the firm’s data also estimates the global car recycling market will reach $244.31 billion by 2032. Factors such as a post-pandemic market and the inflation that followed for items such as labor, fuel and materials weigh heavily in the continuing conditions observed. One industry workhorse that is key in auto recycling is the shredder that can process such a complex product – or metals in general.
Since 1908, American Pulverizer Company has been making size-reduction equipment used by customers in many industrial markets around the world. The firmʼs heavy duty automobile shredders are designed for today’s scrap processor, handling anywhere from 1,000 to 30,000 TPM of automobile bodies – as well as miscellaneous sheet iron, white goods, and more. American Pulverizer shredders are furnished with self-supporting grates, reject doors, hydraulic pin pullers, vibration isolation packages, and an extended skid base for uniting the shredder and feed chute to a common baseplate. “These features minimize downtime and reduce operational costs, making shredders more appealing to businesses aiming for high productivity and sustainability,” James Holder, vice president of sales, stated.
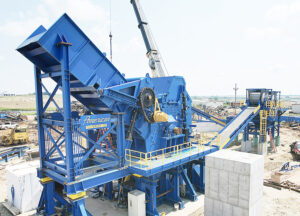
American Pulverizer
A true single-source manufacturer, the American Pulverizer product line includes an extensive amount of machines for scrap processors and other recyclers. This includes hammermills, ringmills, slow-speed high-torque shredders, knife choppers, impactors, trommel screens, jaw crushers, horizontal shaft impactors, and vertical shaft impactors.
Together with their wholly owned subsidiary, Hustler Conveyor Company, they offer complete crushing, shredding, and conveying systems. This facilitates downstream separation processes using magnets, eddy currents, and air classifiers to recover and sort recyclable components. American Pulverizer also provides services such as in-house machining and assembly, rotor teardowns and rebuilds, and spare parts for all types of shredding equipment.
The Forrec dual shaft FX shredder features four gearboxes and four hydraulic motors, delivering exceptional power and torque. Operating at a low speed of three to six rpm, this shredder minimizes noise and vibrations, making it ideal for processing scrap autos. Its patented design includes bolted knives, which allow for easy maintenance and replacement, reducing downtime and operational costs. Power options range from 490 HP to 600 HP and up to 1090 HP, enabling shredding capacities between 10 to 15 tons per hour and 20 to 25 tons per hour, depending on the model. This versatility makes the FX suitable for a wide range of applications, from small and medium-sized scrap yards and vehicle processing yards –where quiet operation is essential for neighborhood compliance – to large metal collection centers requiring high throughput and efficiency.
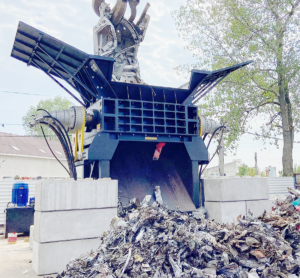
Forrec Recycling
Forrec is represented in the U.S. by the vehicle processing specialists, Vortex. Vortex chief executive officer Nigel Dove said “Compared to traditional shearing machines, Forrec’s dual-shear technology delivers heavy duty structures at a competitive price level. The FX stands out for its high torque, ensuring precise and reliable shredding of even the most challenging materials, while maintaining a cost-effective solution for parts replacement. Through a commitment to innovation and customer satisfaction, Forrec provides not only a technologically advanced product but also an excellent price-to-performance ratio. The FX series shredder is a trusted solution for those looking to optimize light metal and vehicle recycling operations, reduce noise pollution, and achieve high production volumes efficiently.”
Dove concluded, “The FX is hands down the best value for performance ratio on the market. Whether you are processing vehicle scrap or mixed light metals, Forrec’s FX range gives you the best cost per ton available. At the forefront of recycling technology for over 20 years, Forrec offers innovative solutions for light metal and vehicle treatment and the FX dual-shaft shredders are designed for the size reduction of vehicles and light metals, with a perfect balance of performance, durability, and efficiency.”
Zato’s Blue Devil twin shaft rotary shear is a popular solution for pre-shredding car bodies, mainly for hammermills between 500-2500 HP with counter rotating shafts and 60 alloyed blades that cut material at a slow speed of 6 rpm, with extremely high torque. This shredding action produces uniform, dense material that is free of explosive and unshreddable risks, perfectly prepared to go into a hammermill. As a primary shredder, the Blue Devil is used throughout the US to create products like prime, busheling, prepared #2, and hammered shred. Capacity is 25 tons per hour, available in electric or diesel power.

Zato North America
The Blue Shark, Zato’s compact hammermill, provides a smart, reliable solution for creating shredded steel, zorba, and zurik, at a fraction of the cost of other options. With a tight footprint and a hydraulic feeding ram, customers report seeing better liberation and fewer explosions, with a quieter, cleaner system. Capacity is 30 tons per hour with the ability to build modular downstream and the power needed to achieve recovery goals.
“Zato is the premier Italian brand when it comes to shredding, mobile shears and downstream integration. The success that Zato has seen in North America stems from a simple accomplishment – supporting customers’ goals and maintaining near perfect uptime. The biggest growth market we see in North America is aluminum refinement. Operators that can purchase mixed loads and create valuable segregated products are only going to grow over the next 10 years. Our compact hammermill adds processing capability to this operation, allowing users to buy oversized material and produce liberated, uniform metal for sorting. Our largest success lies within our consultation services. With more than 40 years of downstream experience, Zato’s team provides insight into recovery, refinement, and sales of material products. No two recyclers are the same, and a custom, personalized solution is the standard that Zato has set,” commented North American director of sales, Ian Laffey. Zato specializes in metal recycling operations with volumes between 800 to 7,500 tons per month. With American headquarters in Northern Kentucky, the firm services customers in more than half the US states and Canadian territories.
Published in the February 2025 Edition of American Recycler News
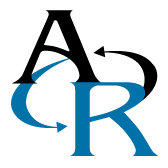