by MARY M. COX
Manufacturer List
|
According to one industry source, it costs about 75 percent less to recycle ferrous metals than to acquire new material. Shredders used to process all varieties of metals are available to assist recyclers involved in the multi-billion dollar industry.
The 3TEK NEXT™ 7400 mobile shredder hammermill system incorporates a Cat® 2,100 hp state-of-the-art mobile “on track” diesel-power module design, with unique power pack options and other modular downstream equipment specifically designed to facilitate ferrous and nonferrous scrap processing close to the source. While also available in a traditional stationary model, the NEXT 7400 mobile hammermill is unique in providing a powerful hammermill design on a mobile platform, with characteristics of much larger hammermills in a compact package that can be fully installed, functional and shredding in three days.
“The industry is changing. 3TEK’s core focus is to provide innovative technology, based upon proven platforms manufactured in the USA, that help small to mid-sized scrap processors take control of growing their business,” stated Bill Padula, vice president of sales for 3TEK Global™ and vice president of Peninsula Equipment.
The NEXT 7400 is the result of a joint venture formed last spring: 3TEK Global incorporates product engineering, manufacturing and product support from three industry leaders, Granutech-Saturn Systems, Peninsula Equipment and Riverside Engineering. 3TEK Global was created to bring the NEXT line of mobile and stationary hammermill shredders and related downstream separation equipment to the small to medium sized yards processing less than 50 tons per hour (tph).
“Unlike other attempts at small-scale scrap processing, the 3TEK design delivers a mill capable of providing very clean, dense, furnace-ready scrap. We’ve leveraged 50 years of shredder design knowledge to create a 74” shredder encompassing the durability and efficiency of Riverside’s Megashredder® product line,” Randy Brace, president of Riverside Engineering explained.
“It’s the best-of-breed scenario. The 3TEK NEXT product line incorporates the hammermill and downstream separation designs of Riverside Engineering, the Caterpillar engines and product support capabilities of Peninsula Equipment and couples them with the 50 years of manufacturing expertise (Big MAC® Crushers) Granutech-Saturn brings to the scrap industry. It’s a powerful combination and we are proud to be a part of it,” commented Matthew Morrison, president of Granutech Saturn Systems.
Next year, 3TEK plans to expand its product line with new, smaller models and matching downstream separation systems.
Sicon focuses on manufacturing innovative and cost-efficient equipment and plants for processing ferrous and nonferrous metals. Since 1998, and offering a unique knowledge in ASR-processing, the firm has supplied a complete range of unique shredding plants for all applications in scrap and metal processing, along with customized downstream plants for total metal recovery.
Jason Silvey, national sales manager, described the Sicon EcoRip as an innovative pre-shredder in 2 versions that processes 50 to 100 tph. “EcoRip helps shredding plants to reduce the environmental impact of shredding and makes smaller shredders more versatile by giving them the ability to use bales or logs. The EcoRip is characterized by a high output at defined particle sizes. The machine can be used as either an effective standalone or it can be added to an existing system. The main shredder offers up to 30 percent increased reliability by reducing wear and tear and decreasing emissions and lowers energy costs (kWh per ton of FE output) when compared with other shredders in the industry. The EcoRip provides improved scrap quality – or higher density – and less copper impurities.”
Silvey explained that the company’s EcoShred® Compact is the most innovative car shredding machine because it combines a pre-shredder and main shredder in one machine with the unique efficiency in the horsepower throughput ratio. The EcoShred is equipped with an integrated pre-shredder, which is implemented as a twin shaft shredder system with a flipper. “The advantages of a pre-shredder and main shredder combo are that scrap is prepared and homogenized for further compaction in the shredder; the risk of explosion is decreased significantly; unshreddables do not enter the shredder, which results in improved operational reliability; peak loads are prevented in the main shredder, so power consumption is uniform; and bales can be processed with a driving power of 1,000 kW,” he said.
Sicon’s EcoShred Vertec is a versatile vertical shredder supplied in four different sizes with a special rotor design for multi-functional applications. From compacting scrap up to exacting degrees, this machine is for throughputs up to 15 tph. Typical applications include: aluminum (castings, profiles, UBC’s etc.), steel scrap (pre-shredded steel sheets, metal drums etc.), meatballs, electric motors, household appliances and generation of nuggets/coolant scrap.
“Our solutions are based on deep practical experience. We learn from our customers so we can provide continuous product and process improvement. Also, intensive research and development projects allow us to implement the latest technology, which benefits our clients. Working with SICON allows them to always be one step ahead,” stated Silvey.
SSI offers a wide range of size reduction solutions for the metals processing industry. “Most of our experience is in preparation of nonferrous metals for a furnace or in destruction of manufacturing scrap such as off-spec parts, stampings or trim. We also have a great deal of experience in processing empty or full containers, electronics and appliance recycling. Our slow speed, high torque shredders and reducers are able to accept large items and bales with ease then reduce them, and meter feed downstream processing machinery at the right rate to optimize plant performance,” Dave Fleming, marketing manager, said.
He said that SSI shredder processing rates range from 1 ton per hour on the small end, for point of generation applications, to more than 30 tons per hour in large baled metal applications. SSI shredders are able to liberate tramp metals or other contaminates during the shredding process so they can be removed from the product stream prior to further processing.
“Many processors choose slow speed processing machinery because of their desire to maximize production rates while minimizing downtime. SSI shredders offer long lasting consumable parts and the slow speed design minimizes the generation of fines, which are a loss to the business and also a potential component to accelerated wear in other processing equipment. When metal prices lag, processors focus on capitalizing on any available opportunity for profit. From a shredder perspective, this means smaller niche machinery that can help ‘upgrade’ the value of a commodity stream by liberating one material from another or creating a consistent product from a mixed stream,” noted Fleming.
Published in the December 2016 Edition of American Recycler News
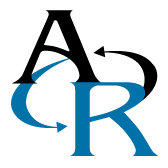