by MARY M. COX
Manufacturer List
|
Among the dozens of occupations analyzed by the Bureau of Labor Statistics (BLS), the 2014 fatality rate of those working in scrap yards was 20.8 deaths per 100,000 full time workers, which is more than 9 times higher than manufacturing workers overall.
Scrap yards, one of the largest segments in the recycling industry, typically report high fatality and injury rates. The BLS also reported in 2014 that garbage and recycling collectors had the fifth-highest fatality rate among the dozens of occupations that were analyzed.
There is no annual record kept of how many workers die across all recycling sectors. At scrap yards and sorting facilities, at least 313 recycling workers were killed on the job from 2003 to 2014, according to the BLS.
FairWarning is a nonprofit investigative news organization that focuses on public health. A FairWarning analysis of Occupational Safety and Health Administration (OSHA) records found that inspections performed from 2005 to 2014 resulted in scrap yards and sorting facilities receiving about 80 percent more citations per inspection than the average inspected worksite. There are many products and services available that can aid employers who must adhere to OSHA standards and who aim to stem the incidence of illness and injury to workers, costly loss of manpower and perhaps even litigation.
Buffalo Turbine manufactures dust and odor control machines which are used worldwide in a variety of settings: Recycling facilities, demolition and construction sites, landfills, aggregate processing and waste transfer stations. “At indoor facilities in particular, visibility and breathing conditions are top priorities for employers who work to keep employees safe from both short and long term harm,” stated Brian Singer, sales and marketing. The turbine units are made using high precision machined components, resulting in long lasting dependable products. Diesel, gas, electric, PTO driven and hydraulic models are available.
The diesel and gas machines are the most popular because they are self-contained and maneuver more easily around a site. “This capability is essential, especially regarding open facilities that are typically affected by the wind. The models also oscillate, which provides a larger coverage area than models that don’t offer that feature.
These machines are convenient due to minimal set up time and this aspect along with simple daily maintenance help aid in smooth production flow. The machines function by introducing water to the gyratory atomizing nozzle (GAN) which uses the power of the turbine air to push the atomized water into the air. This creates droplet sizes of 50 to 200 microns, which matches with the dust particle size and brings the fugitive dust to the ground. Dust control is no longer a trend. It is a necessity for the safety of employees and for adhering to government regulations meant to ensure that those in or near a worksite won’t be impacted by the fugitive dust created there. Facilities can incur large fines if they produce too much dust which also moves beyond their property and a lack of dust control can also significantly slow production,” Singer said.
According to Dave Brentz, Vice President, “Car-Go-Net® provides easy, inexpensive compliance with the Federal Motor Carrier Safety Administration’s (FMCSA) regulations for the securement of flattened or crushed cars.” Cargo Containment Regulation FMCSR §393.132 requires that vehicles used to transport flattened or crushed cars must be equipped to prevent loose parts from falling from all four sides of a vehicle, extending to the full height of the cargo.
“When that rule was first adopted, Industrial Netting worked closely with the Institute of Scrap Recycling Industries (ISRI) to create a safe and inexpensive solution. The result was Car-Go-Net – an extruded plastic netting designed for one-time use. The bright orange color of the netting makes it easily visible to law enforcement so haulers are less likely to be stopped for noncompliance. Our product is lightweight but very strong and the uniform grid pattern of the net won’t stretch or unravel if a strand is cut. In contrast, knitted hay bale-style netting will shred if pulled in a cross direction. The strength of our product allows haulers to wrap material just once to secure their load,” Brentz said.
He claims Car-Go-Net is the most widely used disposable tarp in the scrap recycling industry. In the past 5 years, more than 1,000 scrap processors, auto crushers, metal shredders, salvage yards, towing services and auto recyclers throughout North America, Australia and New Zealand have used Car-Go-Net to prevent loose parts from falling onto roadways during transit. A variety of roll sizes (from 4’ to 17’ wide and from 500’ to 2,500’ long) is available. Also, same or next day shipping is offered on most orders.
Industrial shredders used in recycling and waste markets are run by operators who often rely on vibration, speed, and electrical gauges to determine if the shredder is about to jam, which can then result in worker injury, loss of productivity and other costs. The Lumistar™ high-tech, infeed shredder camera sees through steam, smoke, darkness and past obstacles. This allows operators to see the material approaching the shredder and catch unshreddables and prevent jams when the chute is full, or when there is an autopilot malfunction.
“In deaths per year, the recycling industry is the fourth most dangerous profession in the United States. To protect employees and reduce insurance costs, safety is paramount in shredder operations. When using our Lumistar thermal infrared shredder camera, workplace safety is improved, pollution is reduced and savings improve for electricity and even maintenance. Operators report less wear and tear on their shredders because material is fed properly, so production increases. A specific example of this involves the Corporate Average Fuel Economy standard. It mandates that cars be more fuel efficient, so vehicles are increasingly made with more plastic and less metal. This translates to less profitable hulk value. Our system helps businesses to improve upstream cost per ton,” Paul Angel, President, stated.
He added, “Each camera is temperature-calibrated to the specific environment in which it is placed and our proprietary Steamvision™ technology delivers up to 100 times the resolution of other infrared cameras, through steam. Unlike off-the-shelf infrared cameras made for delicate environments, our shockproof system includes a military-grade enclosure, is completely waterproof and is made from non-corroding, bullet-resistant steel armor. Lumistar cameras have been in use since 2006. Our clients around the globe know that Lumistar cameras are a game changer, giving them a competitive edge.”
RadComm manufactures a product that helps maintain safety throughout the entire metals industry supply chain. Jeff Adams, marketing and sales manager, commented, “Since 1992 we’ve developed the most innovative, highly sensitive radiation detection equipment for small scrap metal recycling facilities to foundries, to some of the world’s largest steel producers. Our products help mitigate risk for our customers and our new NeuSpec and Cricket Magnet systems were designed with that objective in mind.”
The spectroscopic analysis performed by the NeuSpec vehicle monitor automatically rejects or accepts specific isotopes according to customer requirements. For example, a customer can set the monitor to accept all NORMs (naturally occurring radioactive material) such as Thorium and Radium, without alarm. This aid in quickly sorting material helps to increase productivity. RadComm’s Cricket is the only magnet-mounted radiation detection system in the world. It allows scrap metal magnet operators to find radioactive sources from the safety of a material handler cab. Using the Cricket, a potentially deadly, sealed source in a material can be quickly detected and then handled appropriately.
Adams said the company product line includes large scale vehicle monitors to handhelds to laboratory use versions. Custom applications are also available. “The performance of our RC4000 series of products is the metal industry’s benchmark for detecting low level radioactive sources buried in densely packed scrap metal. We’re known for designing and manufacturing sensitive, high quality products that also score the fewest false alarms compared to other products that are similar. In today’s challenging market conditions, our customers often express that revenue lost to rejected loads and/or downtime simply cannot be absorbed. We can provide a solution for any size yard or plant,” he concluded.
Published in the July 2016 Edition of American Recycler News
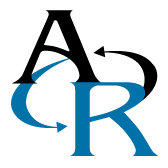