by MARY M. COX
Manufacturer List
|
In the process of recovering metal, the separation of ferrous and nonferrous from other materials can be a challenge. Effective separation can impact factors such as capital expenditures, maintenance costs and ultimately, profit level.
Marshall Gralnick is president of Magnetics Division, Global Equipment Marketing and he cites the most popular recycling magnet type is the self-cleaning overhead magnets. “Since 1988, over 19,000 of our units have been in service worldwide. The magnets are used over the client conveyors, where separation of tramp metal is a necessity to clean up processed materials. Use of the magnets results in threefold benefits, often realizing quick return on investment in a short period of time. They prevent damage to downstream equipment from large pieces of tramp metal. The magnets improve product by removing metal, which results in higher prices paid for cleaner material and last, they eliminate or reduce belt pickers, saving a considerable amount in labor costs.” Gralnick explained.
The firm’s overhead magnets, Mastermags, are available with both electric and permanent magnetics and are furnished with a motor to operate the self-cleaning belt component. Unlike many manufacturers, Gralnick said the company’s range of magnet products is extensive, taking into consideration factors such as customer processing volumes from 5 to over 1,000 tons per hour, conveyor belt widths from 12 to 120”, belt speeds from 10 to over 1,000 feet per minute, material burden depths from 1 to over 30” and size, shape and weight of materials and tramp.
All units are provided fully assembled and ready for installation on a supporting structure (by others) over a conveyor. A quick connection of the motor to the power supply or hydraulics and the magnet is ready to operate without supervision.
Gralnick said few changes have occurred in magnetic equipment over the past 27 years. One event involved premature belt wear, with an initial fix utilizing stainless steel plates, which were added to belts. An innovation in plate construction then led to using high-density polyethylene (HDPE) instead of stainless steel, as HPDE performed just as well, was an eighth of the weight, cost much less and did not require a reinforced drive system. “As the industry continues to evolve, so will the need for different types of magnetic separators. The Mastermag eddy current separator (ECS), for instance, was introduced in 1993 for separating aluminum and other nonferrous metals that were previously disposed of in landfills. The magnetic separation industry is healthy and larger than it was 27 years ago, and will continue to grow with innovative equipment to handle the recycling of metals well into the future,” Gralnick stated.
Repairing or rewinding existing magnets are an effective way to reduce new equipment expenditures by extending the life of existing equipment. Magnetech Industrial Services repairs and rewinds electro-magnetic magnets and designs and manufactures new magnets. David Koch, sales manager, believes it could be a challenging year for the scrap industry. “Scrap steel prices continue to decline and there continues to be an over-capacity of steel. Low crude oil prices will likely further tighten the market. Magnetech serves as a resource for our customers through programs designed to increase productivity and equipment uptime while reducing costly downtime. Clients may also extend the useful life of equipment for a fraction of the cost of new by implementing a comprehensive preventative maintenance program. We offer a best-in-class magnet preventative maintenance program, MagneTrac®. This inspection program covers not only testing of the magnets, but every major component of the magnet system – from the power supply to the controller and everything in between. For over 60 years, we’ve earned the trust and respect of our customers through consistent quality, reliability, timeliness and value for the services we provide,” stated Koch.
He noted that when it is time to upgrade magnets, Magnetech offers both fabricated and cast housing, with circular size from 30 to 95” and rectangular magnets up to 85 x 120”. The sizes and weights of the magnets needed are determined by the crane capacity and the potential load they will carry. The most popular sizes of scrap magnets they offer are 48”, 58” and 67” in the cast magnets and 47”, 57” and 67” in the fabricated models. New designs can be engineered to meet customer specifications as required. Magnetech offers a full two-year warranty for scrap magnets. They also provide spreader beams meeting ASME BTH1-2008 specifications, as well as controllers and the power sources for the magnets which are generators driven by diesel engines or hydraulics. The company also offers crane-operator magnet awareness training, to teach best practices and safe operation of magnets.
Moley Magnetics manufactures scrap yard magnets, shears and grapples. At one point, one of their customers was excavating and screening a scrap yard in an effort to recover ferrous and nonferrous material. As the project began, it seemed the customer would certainly make a great financial gain as a result of the effort. In the end, after having worked part time in just one season, 750 tons of ferrous and 250 tons of nonferrous material were recovered. Since that time, Moley has helped many other clients realize the same financial gains in their scrap yards, by recovering lost metal.
Ron Slaby is the sales manager at Moley and he said, “Considering there is literally millions of dollars’ worth of ferrous material being driven into the ground by non-concrete scrap yards across the world, we thought there had to be a solution to the problem via the use of magnets.
“As a result, the Moley Claw Magnet was developed. This quick-connect, durable magnet system is available in hydraulically driven or 24V driven models. The dual-purpose claw magnet has several innovative features including quick installation, no need for an external generator, fixed mounting and the ability to dig with a magnet.
“While other magnets can only drag across the surface of the ground, the wrist action and fixed mounting of our claw magnet allows the operator to scar the ground and unearth and remove embedded iron. No other magnet allows a user to accomplish this feat. If a grapple is used in an effort to recover metal, the grapple adds soil to the shipment, decreasing earnings for the shipper. The first owner of the Moley Claw Magnet earned the cost of the system back in less than six months! We’re the company to call if you’d like to increase profits at your dirt-based scrap yard.”
Published in the April 2015 Edition of American Recycler News
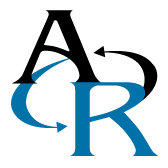