by MARY M. COX
Shredders used in the multi-billion dollar metal recycling industry process materials like iron, steel, aluminum, copper and nickel. Those commodities are then sold to foundries, mills and manufacturers around the world.
Manufacturer List
|
The Taskmaster® Models TM3000 manufactured by Franklin Miller can perform in a variety of shredding applications which demand high power, large throat openings and extra-heavy duty construction. These units employ up to 75 hp motors and planetary gear drives to generate massive force to the cutters.
“They’ve proven their unique versatility and dependability in a wide variety of applications worldwide,” stated James Heyden, sales manager. The heavy construction of the TM3000 features 5.5” heat-treated, alloy steel hexagonal shafting, 2” cam cutters, heavy steel plate and channel body construction. The machine can not only reduce metal items such as steel drums, but can also reduce other materials as well, including: pallets, wood, documents en masse, electronic components, hard drives, hazardous waste, solid propellants, plastic sprues and purgings, tires and other manufactured items. The units are available in throat openings from 30” x 54” up to 28” x 72”.
Granutech offers a wide variety of shredders including single shaft, dual shaft, and quad shaft shredders as well as medium speed grinders – suited for nonferrous recycling applications. Greg Wright, business development manager, explained, “With multiple sizes of shredders in each category, we can meet the needs of small, medium and large processors. Our latest innovation – the Hybrid Drive System – provides maximum efficiency and production in our shredders via constant horsepower abilities. The system automatically adjusts speed and torque in accordance with the load being shredded.
“With this system we provide the ruggedness of a hydraulic system with the footprint of an electric drive shredder. This is especially useful in nonferrous recycling applications when the load seen in the shredder can vary so much at any given time. The hybrid will turn the shafts fast when the load is light but will slow down and increase torque when the load is heavy. The system continuously self-adjusts through the entire torque/speed range, yielding maximum production. Usual processing volume is in the range of 1 ton per hour up to 30 tons per hour.”
Wright noted that many times, customers require a specific shred size that is neither too large nor too small – optimum for their particular smelter – but which also provides efficient separation of materials within the shredder. “It can be a big challenge to identify the right balance of shredding so that a product is small enough to allow for separation, but not so small that losses occur in the furnace. Our Saturn shredders are known for producing small enough product, but with reduced fines. This provides an ideal balance of usable output.”
Wright believes the nonferrous markets are growing as technology allows stronger and lighter materials to be used where steel traditionally has been used instead. “Just look at the aluminum bodied 2015 Ford F-150. I believe you will see much more of this in the future from other automakers as well,” he said.
SSI Shredding Systems offers shredding technology that includes small, 50 hp systems to large 800 hp shredders. “Formulating a good understanding of the customer’s needs – what needs shredding and reviewing the application with an experienced supplier – that is the path to success,” Dave Wilson, industrial sales, advised. Almost all models of each SSI shredder type are used in metal recycling; the two shaft Dual-Shear®, the four shaft Quad®, the single shaft Uni-Shear® and the PRI-MAX® primary reducer.
Wilson said, “Despite the viral popularity of SSI’s YouTube video titled ‘Hippie Bug’, which depicts a Volkswagen Beetle being shredded in an SSI shredder, we do not actually manufacture shredders to process heavy ferrous metal. We do not make a car shredder. A shredder is not necessarily the answer to every metal recycling operation, but there are many applications where a shredder can aid in the recycling of metal.”
Wilson explained that shredding applications can involve aluminum extrusion, baled siding, wheels, steel drums, steel battery cases, incinerated metal, turnings, computers, ACSR, stamping scrap, copper slitter scrap, copper wire, radiators, white goods and computers. “Shredding downsizes the material and often liberates contaminates. The degree of shredding that is required and the type of shredder that would be most effective, all depends on the application involved.
“In some cases, a single shredder is all that is required. An example of that would be one of our recent installations. An SSI Dual-Shear 75 horsepower system was needed in a manufacturing plant for reducing a bulky volume of steel stamping scrap. What started out as oversized bulky parts, or a stamping, was shredded to a uniform 2” strip for improved material handling and recycling downstream.
“If the goal is to separate materials after shredding, then often a small, more uniform particle size is better. To achieve a smaller particle size than a primary shredder produces, double shredding with a secondary shredder is an option. Sometimes a single screen-based shredder such as a Quad or Uni-Shear is more suitable.”
Wilson said that aluminum shredding is a common application for double, slow speed shredding and that materials such as baled UBC, siding, or extrusion are processed on a primary shredder like the Dual-Shear or PRI-MAX. Material is then shredded further on a second, Dual-Shear with a cutter tailored to produce a smaller size.
“The advantages of slow speed technology are many. Maintenance and noise are low. Dust and fines produced are minimal, and equipment on-line reliability is high. Properly designed equipment has excellent shock protection systems. These systems are especially useful when non-shreddables like heavy ferrous are encountered. Satisfactory liberation of material at a reasonable investment can sometimes be a challenge. One shredder is often not enough. A system of multiple shredders and conveyors is often required and the investment can be significant,” Wilson cautioned.
December 2014 Edition of American Recycler News
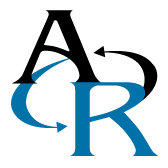