by MARY M. COX
As the practicality of landfill usage continues to wane in fiscal and ecological terms, the practice of extracting metal from tire waste continues to increase.
Manufacturer List
|
Then all materials involved, rather than being discarded, can be recycled. Equipment that can separate metal wire from rubber is a key component in this process.
The Bi-Metal Clean Wire System (CWS) is designed to produce clean tire wire from the tire recycling process. Bi-Metal partnered with Aggregates Equipment to develop the CWS. Bi-Metal Systems has its roots in the scrap metal recycling industry, and Aggregates Equipment, Inc. manufactures systems for the material processing industry. In the early 1990s, Bi-Metal devised a method to recycle wire in a way that also kept the residual rubber at an acceptable level.
The CWS, working in-line with tire recycling equipment, is designed to process the output of a secondary shredder, which performs the task of shredding the wire from the rubber. The CWS process consists of flexible membrane classification, vibration, and magnetic separation. It consumes very little power, requires minimal maintenance, and no additional labor to operate. Two models are available: model 6130 is designed for the output of a single, secondary shredder processing up to 15,000 lbs. per hour, and model 9160 is designed for two, secondary shredders or new, larger capacity shredders processing up to 30,000 lbs. per hour. Customized sizes are available to fit specific customer needs.
“The CWS consistently produces tire wire with less than 2 percent rubber contamination. This is considered the highest quality according to the ISRI specification #278. The first CWS was built and installed in 1997. There are now installations throughout the United States – some located with the largest tire recyclers,” Mark Bielicki, president, stated.
Bi-Metal also offers brokerage services to assist tire recyclers in selling wire produced from the CWS. The Bi-Metal staff offers vast experience in the scrap metal recycling business and they can assist tire recyclers in securing the best possible price for recovered wire. “Steel mills today are looking for competitively priced scrap to meet strict quality standards. Some steel mills prefer tire wire to be loose, others want it baled and some are unable to use it in any form at all,” said Bielicki.
He expects market demand for this technology to continually increase. “More and more, tire recycler end markets require increased production of ‘wire-free’ product, and landfill disposal is becoming an unacceptable option for both economic and environmental reasons. Steel mills are more accepting of tire wire as a scrap feedstock and this trend will continue as long as tire recyclers can produce a reliable, consistently clean tire wire product,” Bielicki explained.
CM Tire Recycling Equipment offers a broad range of systems for the reduction and reprocessing of scrap tires. Kaytee Moran, equipment sales, noted, “From shredding to fine grinding of rubber CM is the world’s leader in the tire recycling industry. The CM Zero Waste System includes a CM Liberator and CM Steel Reclaim System. The Liberator will process 4” to 6” pre-shredded tire material producing a variety of rubber sizes. Depending on capacity, a CM2R or CM4R Liberator can be used.”
According to Moran, after material is discharged from the Liberator, the CM Steel Reclaim System efficiently screens and separates the comingled steel and rubber that is generated from the tire recycling process. The material value can be greatly enhanced by this additional processing. The system utilizes a special vibratory cleaning screen in combination with two magnetic separators to reclaim all steel and rubber. Depending on screen size, the 4R Liberator system is capable of processing passenger car and truck tire material at production rates ranging from 4,000 to 20,000 lbs. per hour. The 2R will do half the production of the larger 4R.
The CM 2 and 4 Rotor Liberator has a serrated knife design which gives each knife more linear inches of cutting surface. “The larger cutting surface means less time is needed to process tire material, thus lower energy consumption. The Liberator’s over-sized screening area permits efficient screening and separation of wire and rubber. This product also offers an exclusive ‘armor-plated’ rotor and rotor housing, which dramatically reduces wear to internal components. Internal wear surfaces are lined with replaceable wear liners that are easily changed when worn. This exclusive feature of the CM Liberator results in greater machine uptime. When used together, the CM Liberator and Steel Reclaim System will give you the most profitable, zero-waste scrap tire processing capabilities in today’s market,” Moran concluded.
“ECO Green Equipment provides the full solution for scrap tire recycling and processing. Since 2010, we’ve designed and manufactured equipment for the recycling industry and we’re emerging as a leader in providing cost-effective turnkey tire recycling systems,” stated Brad Swenson, manager.
He explained that the key to the firm’s equipment line-up is the ECO Grater. “This unique piece of equipment separates the steel from rubber tires and removes up to 99.9 percent of foreign objects in order for the operator to sell or re-use the steel. Steel is in high demand for use as an additive for burning in smelters and in other energy-related industries. The ECO Grater is specifically designed to take pre-shredded tire chips and produce between 1.75” and 0.5” rubber chip for other uses. The machine can process up to five tons of rubber input per hour. The main rotor housing is equipped with replaceable wear plates to increase the durability and longevity of the cutting chamber. It features a knife rotation option, which allows the cutting knives to be turned once before sharpening or replacement is required.”
ECO Green Equipment also provides a full lineup of single and two-shaft shredders, separation, granulation and rubber milling equipment. “Our patented, hydraulic-powered ECO Krumbuster® is the industry standard for commercial grade cracker mills. Our management and engineering teams provide custom-designed tire recycling systems that deliver optimum production for a variety of rubber applications such as tire derived fuel, wire-free chips, crumb rubber and rubber powder,” Swenson added.
He said that ECO Green’s mission is to provide customers with a competitive advantage. They do this by using proven technology and components in combination with sophisticated testing equipment that ensures all equipment meets industry standards. Each system is tailored to the needs of the business location, market, and customer. ECO Green products are in operation all over the world.
Published in the July 2014 Edition of American Recycler News
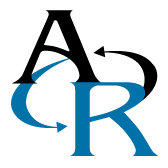