by MAURA KELLER
Within the metal recycling process, there is a vast amount of “waste” produced that simply can’t be ignored.
“Metal is a reusable and valuable resource. It’s important to recycle metal not only for the environmental and economic impact, but also to prevent metal being present in ground water supply,” said Mikel Shecht, executive vice president, Geomet Recycling. “We take the mandatory steps and have processes in place to ensure that the waste our facilities produce is properly disposed to lower the impact on community landfills and the environment at large. Like many other industries, the technology used in waste facilities is evolving quickly.”
Geomet Recycling, for example, receives different types of packaging materials in the form of cardboard boxes, pallets and steel strapping and banding. The company has arrangements and partners set up to recycle the paper products from packaging, a pallet service/rebuilder/recycler, and they thoroughly inspect and make sure all metal packaging is recycled.
Shecht said there are some byproduct waste materials, for example, the plastic that comes from the casing of aluminum and copper wires that they recycle. Geomet Recycling has been looking for ways to give a second life to such items by partnering with companies that can use it as raw material or in products they manufacture.
Another area of metal waste that requires recycling is rare earth magnets. Geomega Resources recycles rare earth magnets, a new type of metal waste that is growing in volume and importance.
According to Kiril Mugerman, chief executive officer, Geomega Resources, until recently, magnet waste was being discarded together with regular metal and steel scrap that was destined to be shredded and then melted in large furnaces.
“Metal and steel scrap is low value but large volume. The waste it generates is of even lower value and there is significant metal value loss,” Mugerman said. “In the case of Geomega’s process, we are able to capture the rare earths that are otherwise completely lost in the traditional metal recycling industry.”
As Mugerman further explained, it is critical to recover rare earth magnets separately from the traditional metal scrap heading for melting. The ability to capture rare earth metals provides several advantages:
•Additional revenue for the metal recycling industry, allowing them to increase their collection sources.
•A circular economy for these critical and strategic metals.
•Local production of rare earth elements from material, originally mined and produced in China.
“We saw China make the necessary adjustments in the beginning of the previous decade,” Mugerman said. “Today, it is believed that 30 percent of the rare earths that go to magnet production are coming from magnet recycling. We have seen an incremental growth in R&D of more environmentally friendly approaches to recycle rare earths from magnets and Geomega has been actively involved in it since 2017.”
Technological Progress
The recycling and waste industries have made substantial advancements over the last 20 years. As Shecht explained, mechanically, those advancements continue to improve. A key focus of the metal recycling industry is to isolate and separate many commodities (often mixed together, from metal, to plastics, paper, and aggregate) to allow each of these commodities to find their way back into the usable stream rather than into landfills.
“Lightning quick magnetics, vibration, screening, color sorting, chemical analysis, pneumatics and density separation equipment exists and continues to improve. We are excited to see what is coming next,” Shecht said.
Indeed, to make the technology competitive with the process in China, Geomega had to develop a process where not only are rare earths recovered but also iron, in a salable form, and all major reagents.
“By making the process practically zero waste, the technology becomes competitive and environmentally sustainable, which is a must in today’s ESG environment,” Mugerman said.
Metal Waste Within Lithium Ion Battery Recycling
One area of metal waste recycling that is gaining attention is the recycling of lithium ion batteries and their metal waste components. David Regan, vice president of commercial at Aqua Metals, said Aqua Metals’ proprietary AquaRefining process relies predominantly on renewable electricity rather than high heat or chemicals to recycle, which results in a significantly cleaner process. The few chemicals we do used within the firm’s closed loop process are recycled, producing a reduction of 97 percent in the chemical waste stream.
In comparison with other lithium-ion battery (LiB) recycling processes, the AquaRefining process is by far the cleanest approach. For example: pyro-based recycling produces 4212 kilograms of CO2 for every metric ton of black mass processed. Black mass is a type of e-waste comprising of crushed and shredded battery cells and contains mixtures of valuable metals including lithium, manganese, cobalt and nickel.
“In comparison, one metric ton of black mass processed through standard chemical hydro has a 2,960 kg of CO2 footprint. This is significantly better than pyro. Nonetheless, the process generates nearly three metric tons of CO2 for every metric ton of product,” Regan said.
“In contrast, Aqua Metals’ internal estimates indicate that AquaRefining produces 65 kg CO2 emissions for every metric ton of black mass produced. That converts to 0.065 MT per 1 ton of black mass – a roughly 98 percent reduction in CO2 over both pyro and hydro.”
So why is the amount of emissions produced from the black mass recycling process important to the metal waste recycling segment of the industry? Quite simply, as Regan explained, “the sheer pending volume of spent LiBs expected to enter the market in the next decade (TechCrunch forecasts 15 million metric tons (MT) of spent LIB batteries by 2030) means that is vital right now to build a cost-effective, scalable recycling infrastructure that is environmentally sustainable from inception.”
Many mainstream recycling companies rely on either pyro, also called smelting, or traditional hydro processes, both of which have unsustainable environmental footprints when applied to significant volumes of recycling.
“The former results in unsafe workplaces, emitting more than two tons of greenhouse gasses per ton of batteries smelted as well as other pollutants, while losing high value minerals like lithium and manganese in the process,” Regan said. “The latter produces a toxic chemical waste stream, considered by the EPA as harmful to human health, aquatic life, and the environment. Chemical waste streams need to be treated and landfilled properly, which incurs significant cost.”
Unlike standard hydroprocessing, AquaRefining is an emissions-free, room temperature process. All chemicals are recycled, eliminating chemical waste and the purchase of expensive replacement chemicals. AquaRefining essentially builds metal by electroplating one atom at a time.
“Our process starts from the black mass which is a result of the breaking and separation and crushing of the lithium cells to begin with,” Regan said. “We take that black mass as the input to our process, and we begin to work with that black mass through the use of chemicals that are in that closed loop. The electricity is the catalyst that allows us to separate out and then selectively plate key minerals in metal form. While AquaRefining is still in development, Aqua Metals is making steady progress toward taking it beyond the idea stage and into the best solution for recycling lithium-ion batteries.”
Looking Ahead
Recycling and waste companies should pay close attention to the always changing supply stream as product composition, uses, and forms are always evolving, thus affecting the amount of waste produced in the metal recycling process.
As Shecht pointed out, recycling and waste companies are on the front line of identifying these new streams and the opportunities to improve processes and reduce landfill waste.
“The producing industries and the recycling and waste industries can work closely together to engineer with the intent to recycle,” Shecht said. “Robotics, software, AI, camera improvements and energy efficient solutions are exciting opportunities for our industries and communities. Hiring and company culture will have massive impacts on the success of these advances. Passion drives innovation and improvements.”
Mugerman added that today’s recycling companies are living in an evolving recycling world. We saw a few of these transformations over the last 120 years as usage of various metals increased and recycling companies had to adapt.
“Today, we see that more and more critical metals are being used that present new value opportunities,” Mugerman said. “Therefore, as concentrations of these critical and strategic metals increase, what was considered waste from the metal recycling industry is becoming a new recycling stream that the most creative recycling companies would be able to capture and benefit from.”
Published in the November 2022 Edition
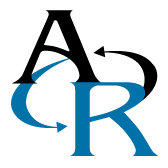