by MARY M. COX
Manufacturer List
|
The eddy current separator (ECS), first introduced in 1984 in Europe, is an automated method for separating nonferrous metals, such as aluminum and copper, from domestic and industrial waste. Prior to this invention, these metals were sent to the landfill, causing contamination and wasting valuable commodities and resources. The evolution of the ECS over the past 30 years has resulted in the machine often being a staple at recycling facilities across the world.
Dings Company is a 117 year old manufacturer of a complete line of magnetic separators that includes electro and permanent overhead magnets, magnetic drums and head pulleys, plates, grates and eddy current separators. Mike Vukovic, account manager, explained the details involved in the performance of these machines: “Material is fed onto the conveyor belt of the ECS, which moves it across a magnetic rotor where separation occurs. The two streams of material discharge into a housing. The housing has a splitter to divide the nonferrous metal from the nonmetallic material, such as paper, plastic, wood or fluff. The key component of the ECS is the magnetic rotor, which has a series of permanent rare earth magnets mounted on a support plate attached to a shaft. The magnetic rotor is surrounded, but not attached to, a wear shell which supports the conveyor belt. This allows the rotor to spin independently and at a much higher speed than the wear shell and belt. When a piece of nonferrous metal such as aluminum, passes over the separator, the magnets inside the rotor rotate past the aluminum at high speed. This forms eddy currents in the aluminum, which in turn create a magnetic field around the piece of aluminum. The polarity of that magnetic field is the same as the rotating magnet, causing the aluminum to be repelled away from the magnet.
This repulsion makes the trajectory of the aluminum greater than that of the nonmetallic, allowing the two material streams to be separated.” Vukovic said that Dings’ rotors are made with a triple layer shell. The triple shell layers of ceramic tile, fiberglass and heavy duty stainless steel, protect the magnetic roller assembly. This aids in providing a longer life for the machine and lower maintenance and repair costs. Dings’ three sizes of eddy current separators can process up to approximately 25 tons per hour.
Vukovic commented on the fact that recyclers’ fixed costs are affected by processing material prices and market value fluctuates for commodities like aluminum, steel, paper and plastic. “Aluminum imports, for example, affect the price for recycled aluminum—which is down approximately 30 percent from last year. When markets are down recyclers need to spend less time sorting material. There is also an increasing demand for a cleaner, less contaminated end product.”
Mastermag units, manufactured by The Magnetics Division, Global Equipment, were first introduced in the late 1990s. The Mastermag product line now offers a full range of products, including: the CanSorter, specifically used for aluminum can sorting; the MasterSort, fairly new to the market, with a high speed eccentric rotor design, which separates ‘fine’ nonferrous metals from other materials such as glass cullet, shredded wood and electronic scrap. Marshall Gralnick, president, said, “The MasterSort also includes a new material splitter plate design, allowing for complete adjustment flexibility and precise material segregation. With rotor speeds of approximately 3,000 RPM and using rare earth magnetics, our Mastermag ECS machines are suitable for any type recycling plant with volumes from 1 TPH to upwards of 250 TPH and more, utilizing multiple systems in tandem. Although ECS systems are complicated machines designed for specific purposes, the ease of set-up for a Mastermag is remarkably simple. In most instances, a factory specialist is not required.
“Our system assembly requirements are as simple as a ‘plug and play’ game. All wires or cables are color-coded to match the same color receptacle involved. The adjustments and instructions required are easy to follow using our manual, with easy to follow photos and diagrams.” Gralnick noted that the key to growth of the ECS in recycling lies with commodity pricing, “Prices for copper and aluminum, as well as many other metals, have been deteriorating to near all-time lows, as a result of market demand from China. While this trend may continue for the immediate future, eventually prices will begin to rise again, as China sorts out their market and the demand for recycled materials is reignited. In the meantime, the ECS will still be an important tool in metal recycling and will continue to evolve.”
According to Steinert U.S., 65 percent of eddy currents used today in the scrap industry are Steinert machines. Bart Kocik, vice president of sales stated, “Our NES eddy currents have historically been the workhorse of the industry, and we continue to innovate. This is evident with the success of our NES 4T, which separates nonferrous metals from extremely fine fractions, delivering a higher yield and longer life than other machines that perform a similar function.”
“Steinert pioneered and is now the leading manufacturer of eccentric pole system eddy currents. The NES 4T has more magnets than any other eddy current on the market – making it stronger at 4000 RPM than competitor machines that run at higher RPMs,” he said. “The eccentric pole system allows for maximum ejection efficiency, and residual ferrous metals cannot adhere to the head drum, which reduces damage to both the belt and drum shell. It is one of the most adaptable and durable pieces of equipment available.”
Kocik also reports that the NES 4T has variable belt speeds to adjust to the material being sorted, pre-programmed options and a 24-month warranty. All Steinert eddy currents have a standard 24-month warranty. The product is available in four sizes: 1m, 1.5m, 2m and 2.5m, with a belt speed of 1 to 2.5 m/s. “The scrap, waste and recycling industries do their best to extract the purest form of every commodity available during the sorting process. As a result, companies seek equipment that can remove the highest percentage of commodity product possible, and as quickly as possible. Our equipment set the bar to achieve just that,” Kocik commented.
Published in the April 2016 Edition of American Recycler News
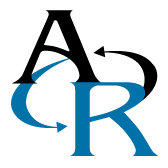