MANUFACTURERS3TEK Global American Pulverizer BCA Industries Franklin Miller Granutech-Saturn Systems Hammermills International Harris Waste Management Group Komar Lindner Recyclingtech America LLC Metso Metal Recycling Riverside Engineering, Inc. Shred-Tech Sicon America SSI Shredding Systems, Inc. UNTHA Shredding Technology Inc. Weima America, Inc. |
The EPA estimated the recycling of ferrous metals to be 27.8 percent (4.7 million tons) in 2018. Shredders are a dominant product used by the recycling industry in processing efforts.
3TEK offers a totally new shredding option for small yard owners who want to increase their shredding operation. “With a full owning and operating cost less than $35/ton and with an output of up to 3,000 tons a month, 3TEK’s Bravo will raise your capability and your profits, putting you in command,” advised Bill Padula, vice president of sales and marketing.
Driven by a 1,125 hp CAT32 Tier 4 certified diesel engine, the Bravo can comfortably produce 15 to 20 output tons per hour. This mobile, massive, 311,000 lb., single-chassis machine sports 240 lb. hammers and comes standard with an integrated 19’ infeed conveyor and compact pin puller assembly.
“The Bravo has been designed from the ground up to process scrap. This is a true hammer mill that delivers very clean, dense, furnace-ready scrap at a price point for both purchase and production that makes sense for small yards,” said Padula. In partnership with 3TEK, the shredder is designed and manufactured by Riverside Engineering, Granutech Saturn Systems, and Blanchard CAT. Dedicated 3TEK technicians take pride in their responsiveness, as products are manufactured in Texas and their South Carolina warehouse is fully stocked with wear and spare parts.
For recyclers of a wide range of metals, BCA Industries has developed the customizable ES2000 shredder, called the “Beast.” The machine features a proprietary hydraulic cluster drive system that can handle the toughest shredding applications to shred ferrous and nonferrous metals and electronic waste in both stationary and portable units. With 24,000 and up lbs. total gross weight (including power supply), it is designed to shred 15 to 35 tons of metal per hour. The variable displacement hydraulic feature is a key differentiator, allowing the rpm to automatically adjust up and down to load requirements. Other features include 24” diameter hard-faced knives, 55” to 72” x 44” cutting chambers, and 8” 4130 Chromoly steel shafts. When even more power and production are required, the Beast can be rated up to 800 hp, and utilize dual cutting chambers. John Neuens, sales and marketing director, said the shredder can make short work of even the largest metal scrap items.
BCA Industries was formed in 1998 by twin brothers Doug and Joe Bartelt, who grew up welding, fabricating and designing machines with their father, a machine designer and shop owner. They now oversee their firm from a 23,000 sq.ft. facility on 3.5 acres in Wisconsin.
Granutech-Saturn Systems makes several types of shredders for nonferrous or light ferrous applications, including rotary shear shredders and the firm’s Roto-Grind and Grizzly Grinders. “We recommend the best shredder option, depending on the characteristics of the material to be shredded, the required output and the number of tons that must be shredded, per hour. Sometimes the application requires two machines in a series, such as a Saturn Dual Shaft shredder for initial reduction, followed by our Grizzly shredder, for final reduction. For a customer seeking a dedicated ferrous shredder for automobiles and light iron, we refer to our partner company, 3TEK, as they specialize in mobile hammermill shredders and downstream separation systems,” Greg Wright, vice president, stated.
The firm’s clients may typically process about 4,000 lbs. per hour all the way up to running 24/7/365 with shredders capable of processing 40 tph (of aluminum).
Shredders manufactured by Granutech-Saturn Systems process metals such as steel barrels, radiators, cast aluminum, used beverage cans and more. Proper maintenance is imperative for optimal operation, and Wright recommends keeping a shredder clean and properly greased, keeping cutters sharp, and regular maintenance for the hydraulic system. He cited an uptick in metal pricing making it a good time to consider shredding and separating metals. He concluded, “Our company roots began in the late 60s, making automobile crushers. After acquiring Saturn Shredders in the late 70s, we began offering shredding solutions for various materials in a variety of markets. We’ve continued to grow and diversify ever since.”
Harris sold its first shredder in 2001 and since has sold 30 more, across the globe. Harris shredders range in size from an economical 6090 shredder driven by a 1500 hp motor, producing 30 tph, all the way up to a massive 125125 shredder, driven by a 7000 hp motor, producing almost 300 tph.
“Due to scrap market volatility, ferrous shredder operators strive for a low operating cost per ton. As incoming scrap and outgoing ferrous prices fluctuate, it is imperative that a shredder runs in the most efficient manner, to maximize profitability margins for the shredder owner. Optimal shredder plant efficiency depends on maintaining sufficient, on-hand spare parts, scheduled maintenance outages, adequately trained personnel for operations and maintenance, a steady influx of scrap material, safety protocols and the ability to react to the unexpected, in a positive way,” commented Philip Walls, director of shredder operations.
Walls also mentioned how acquisitions and consolidations have idled some shredder plants and sales of new shredder plants have slowed. This trend has heightened the value of maximizing the production of current systems. The upgrade or retrofit of older shredders, using newer technology and better designs, has increased. Operators are achieving higher production using older shredder plants by engineering upgrades for existing machines. Components of the shredder system are replaced with newer, more efficient designs that involve the rollers, feed yoke frame/rollers, infeed conveyor, motor/drive packages, PLC/HMI and more. As a result, older shredders may achieve a 10 to 20 percent gain in production, with just a moderate capital investment by the owner.
For over 100 years, Harris has manufactured recycling and scrap processing equipment, including various models of shears, balers, shredders, rotors and infeed conveyors, all engineered and manufactured at the Harris facility in Georgia.
Sicon America offers a full range of pre-shredders as add-ons for existing shredding plants. Heiner Guschall, chief operating officer explained, “The EcoRip Neo 200/250, with a throughput range from 40 to 120 metric tons per hour, offers the perfect shredding solution for any user who seeks to increase production by 20 to 30 percent, avoid explosions and power peaks as well as reduce wear cost in the main shredder.” The fully automated, heavy duty pre-shredder employs a patented drive system and segmented rotor design for a virtually endless rotor lifetime. EcoRip Neo was designed for the lowest operating cost and quick, simple installation. Automation and hydraulic systems are pre-installed and pre-tested in a container so the machine can be used within a few days of delivery. Sicon’s automation engineers will also adjust the main shredder’s software to ensure smooth setup and estimated ROI is less than 24 months.
The firm also offers a full range of customized shredders, including the EcoShred Vertec, for the processing of meatballs and electric motors as well as coolant scrap (in a different setup) and Guschall noted that these products offer an extraordinarily low operating cost. Sicon’s EcoShred Slimtec (up to 800 hp) and Compact (up to 1500 hp) are helpful scrap processors for small to medium shredding needs.
Published in the April 2021 Edition
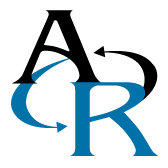