by MARY M. COX
Manufacturer List
|
Genan, which claims to be the world’s largest tire recycling company, reports that an estimated 13.5 million tons of tires are scrapped annually. The global market offers recyclers a wide range of products that are available for use in the effort to continue the lifecycle of scrap rubber.
Columbus McKinnon (CM), a leading manufacturer of tire specific processing equipment for the tire recycling industry, recently developed a new line of hybrid shredders for the general and mixed waste and recycling industry. The new line consists of shredders from 10 -250 hp(7.5 – 185 kW) with feed openings as small as 30” x 18” up to 90” x 46” (76 x 46 cm up to 229 x 117 cm) and are offered with traditional one piece shear knives or CM’s new patented replaceable knife inserts.
Offering numerous improvements, the machines include advance knife locking systems, bearing protection and PLC controls. The crowning advancement is CM’s new cutting technology. This proprietary knife system has been used in the company’s tire shredding machines for the past 35 years. The high quality steel found in tires requires that knives be made from a high grade, hardened tool steel to effectively cut the steel wires cleanly. This same technology can be used for other high wear applications in the mixed waste and recycling industries. The knives, available in numerous sizes and configurations depending on the application, can be rotated and re-sharpened numerous times for multiple uses. This is a cost effective option, compared to welding and the replacement of entire rotors.
Tom Schroeder, director of sales and marketing, explained, “This advancement in knife technology can reduce knife costs by over 300 percent and downtime associated with knife changes. By replacing knife inserts, it is not required to dismantle the machine to replace the knives. In some cases, this could reduce knife change time by 50 percent. Also, in most cases CM can adapt existing shredders of all makes and models to their new knife system. This allows the processor to take advantage of this new technology without replacing their existing shredder. CM holds numerous patents based around cutting, screening and separation technologies for tires, one of the most difficult products to recycle. Customers can send material to CM for testing in one of many shredders. The process can be viewed in person or CM personnel will video record all tests for later client use.”
ECO Green Equipment is a leading specialist in the design and manufacture of industrial grade tire recycling equipment and the firm offers a primary tire shredder, the ECO Green Giant. The machine, a two-shaft primary shredder exclusively engineered for processing whole scrap tires of all sizes, features a low RPM, high-torque technology. It efficiently shreds whole tires into rough rubber shreds (8 – 2” inches) for use or further downstream processing.
“The product is very popular with our clients as it’s the first station in the tire recycling process. Processors can insert whole tires into the Green Giant and output tire shreds for TDF (tire derived fuel), TDA (tire derived aggregate), and other similar sizes for energy, engineering, and other secondary applications. If smaller sizes of rubber chips are desired, additional equipment and connecting conveyors are available as add-ons. Production rates for this primary tire shredder are estimated at up to 30 metric tons of tires per hour, depending on output size required,” Brad Swenson, managing partner, stated.
Swenson reports that the patent-pending triangular Green Giant blade configuration provides up to six times the life of a traditional shredder blade before sharpening is needed. Each knife has six edges, which can be sharpened up to 1x for a total of 12 edges per knife before replacement.
“Processing operators typically want to identify the cost to purchase, operate, and maintain reduction equipment. Depending on the desired size of material output, processors also want equipment versatility. Output size also dictates the amount of processing time, wear, and energy consumption. Recycling facility operators prefer equipment that is efficient, low maintenance, and with overall low operational costs. Accommodating customer needs can be a challenge but we see high demand globally, for scrap tire size reduction. Many industries seek smaller tire derived aggregate or chips for numerous uses. Industries such as construction, sport, and energy sectors use TDA as a replacement for natural resources previously used. Civil engineers and construction companies seek primary reduction output from tires for infill and construction material.”
“Processing OTR tires, which are used in a variety of mining vehicles, can be extremely difficult and costly to manage. Mining organizations sometimes bury scrap tires to dispose of them. Alternatively, we can recommend unique procedures and equipment to shred and recycle these large tires. New uses and products are being developed every day for rubber and tire recycling. The more these markets are developed, TDA demand will increase,” said Swenson.
Eco Green serves the global market and seeks to establish new markets with government, business and organizations that desire to improve their communities and environment. ECO Green Equipment has offered tire recycling equipment exclusively for the past 8 years and assists customers with a full-service package of equipment, training, and support.
Eldan Recycling has recycling solutions for processing of all types of tires; whole car and truck tires —including for mining, super singles, earth mover tires, OTR and more. The capacity of systems offered range from 1.5 – 8.0 ton/production per hour. “To achieve the required end product, various standard tire recycling plants are available. These standard plants are also the starting point when systems are tailored to suit specific customer requirements. Our systems are ‘multi-size’ meaning, the size of rubber granulate easily can be changed by merely altering the screen size combination. Using a modular approach, a large number of combinations can be supplied to produce shreds, chips, granulate and powder. During production of rubber granulate; flexibility is a very important factor since the market demand of various fraction sizes varies. Eldan’s tire recycling solutions offer the highest production output quality and flexibility, as well as lowest operating and production costs. The tire recycling market is strong but at times, finding enough used tire scrap and identifying end user needs can be a challenge,” Ken Moulin, sales manager, commented.
Eldan products for size reduction include the following: The Super Chopper is a powerful, low speed single or dual shaft pre-chopper, capable of processing complete car and truck tires including super singles, down to shreds. The multi-purpose Rasper is an effective, medium-speed, dual drive machine. The product ensures individual size reduction down to approximate 12mm chips and liberation of up to 98 percent of steel content. The Fine Granulator #1 is a high speed, single shaft fine machine for the first granulation stage, enabling liberation of up to 50 percent of the textile contained in the tires. The textile material can then be removed by the Classifier PC10.
The Fine Granulator #2 is a high speed, single shaft fine granulator for the second and final granulation stage. If needed, any remaining steel and textile can be liberated and the steel is removed by magnets. The Classifier PC15 removes 40 percent of textile material. The Aspirator ensures the final size distribution of granulate and removes any remaining liberated textile, providing a high quality rubber granulate, with purity of up to 99.9 percent.
Published in the August 2017 Edition of American Recycler News
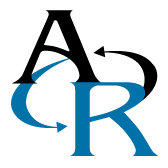