ManufacturersBCA Industries CM Shredders CW Mill Equipment Co., Inc. Eagle International Ecoverse Industries Eldan Recycling Gradeall International Ltd Granutech-Saturn Systems M&J Recycling SEDA Environmental LLC SSI Shredding Systems, Inc. Tana North America Untha America
|
The global market growth for scrap tire management and rubber remediation applications was projected to reach nearly $9.5 billion by 2022, according to BCC Research. Scrap tires, the largest portion of rubber refuse, contains many resources and thus offers great flexibility when it comes to recycling potential. They can be reduced to their constituent elements of wire, fabric and rubber, and then used as fuel or in civil engineering projects such as road building. As this overall market continues to grow, these manufacturers provide a wide array of equipment for use by recyclers.
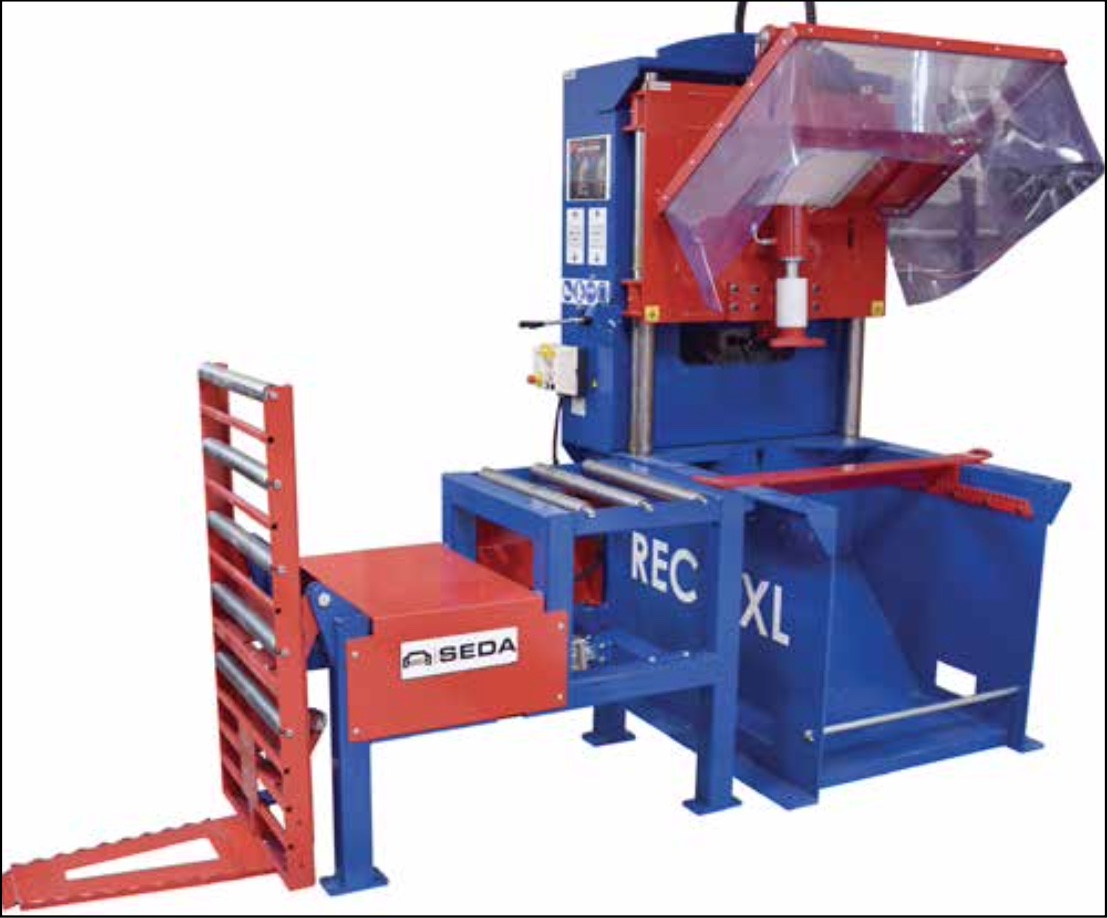
SEDA Environmental LLC
Gradeall’s tire recycling products include the MKII tire baler, a tire rim separator, portable and static waste compaction systems, a sidewall cutter and tread cutter. The company offers a tire processing product for agricultural settings as well. “Our products help to make tire disposal easy and cost effective, regardless of the scale of your recycling operation and produce a 850 to 900 kg tire bale, that can be shipped in a 40 ft. container to tire pyrolysis plants and tire producers all over the world.,” stated Stephen Murphy, managing director. With a force power of 45 tons, Gradeall’s MK2 tire baler can process 4 to 6 PAS108 bales per hour and reduce overall volume by 80 percent, with each bale containing up to 110 tires. This baler, is optimal for baling car tires, but also processes truck tires easily, if they are first processed via a sidewall cutter.
The Gradeall MK3 tire baler system employs 75 tons of powerful pressing power. The result is the ability to form three bales per hour, each taking approximately 20 minutes and containing up to 140 tires, depending on their average size. The Intelli-Link feature of the machine provides wireless connectivity to operators, which monitors performance and reports on various, helpful operating factors in real time.
The MK3 can be equipped with Gradeall’s baler conveyor (capable of feeding two balers), which saves on the time and effort exerted by operators in loading the MK3. This step also helps in reducing the overall time needed to load and unload bales from containers. The Gradeall truck tire baler produces bales containing up to 12 truck tires and the baler’s 50 tons of force reduces tire volume by 60 percent while using a system that also easily ejects completed bales.
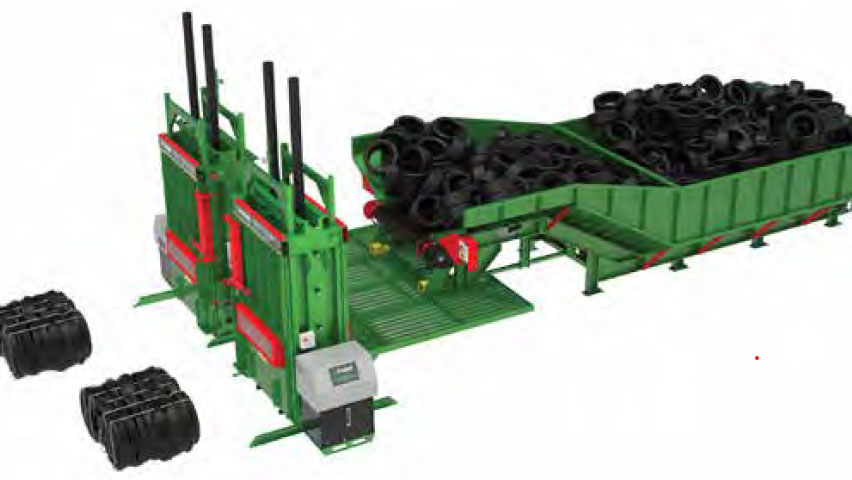
Gradeall International Ltd
Murphy concluded, “Our tire baler conveyor, an excellent add-on to our MK2 and MK3 tire balers, can be installed to help reduce baler loading time and the physical demands of performing the work manually. Operated using two hands, the machine allows for maximum control, and our tire rim separator is surrounded by guards to protect operators and prevent the scatter of debris.”
Greg Wright, vice president of Granutech-Saturn Systems explained, “We offer over 50 years of manufacturing size reduction equipment for the recycling industry. Tire recycling continues to be a very large segment of our sales and I don’t see this changing any time soon. The equipment we manufacture and recommend for tire recycling can vary greatly depending on the customer’s requirements. Depending on the final product size required, processing rates can range anywhere from 1,000 lbs./hr. to 20 tons/hr.” Wright added, “If a customer only wants to make a primary shred or a chip, we would recommend one of our dual shaft shredders, possibly with an external sizing screen, or a quad shaft shredder. If the goal is to reduce tires to a powder, then four stages of processing with various pieces of equipment at each stage are involved, performing various tasks. Reducing tires to crumb rubber is much different than performing a primary shred or chip, as removing the steel and fiber becomes a large part of the process, at different stages and with a variety of equipment.”
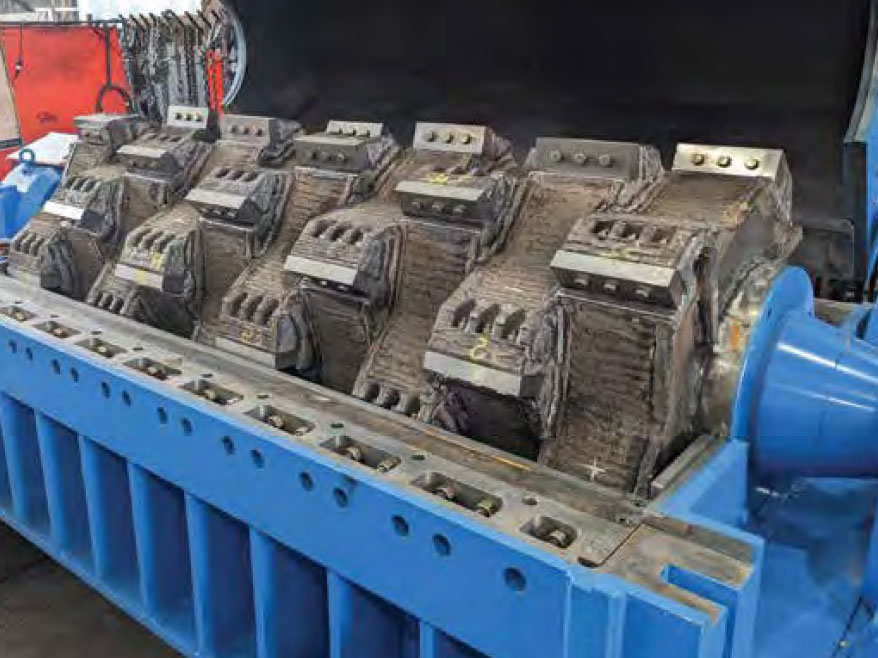
Granutech-Saturn Systems
The SEDA T-REC XXL separates tires and rims, fast, safe and efficiently, according to Bruce Henderson, chief executive officer. “Tried and tested, it separates steel or alloy rims from 13” to 22” with ease by bending or snapping the bead off the rim, pinching and puncturing the tire and then slipping the tire off the rim, separating both by brute force. This process guarantees separation of almost all tire and rim types, including smaller ‘bring me home’ wheels and run flats,” said Henderson. The T-Rec XXL comes standard with laser aided wheel alignment for easy wheel placement and a self-raising shield to protect the operator from any possible shattering of alloy rims. The unit is also available in a 230V 3-phase electric version with a full cycle time of 35 seconds, and the latest gas-powered version with key start boasts a full cycle time of less than 20 seconds. Both units ship fully assembled, direct from SEDA.
Henderson explained how SEDA’s latest innovation – the T-Rec XXL feeder, helps load a stack of wheels on the tire machine, which increases the ease of machine use. This new wheel feeder fits the electric and gas powered versions of the T-REC XXL and advantages of using the two products in unison include: steel and alloy rims from 13 up to 22” accommodates for all kinds of tires (including run flats); fast, safe and efficient processing; laser aided wheel alignment and gas or 230V 3-phase electric options.
Published in the August 2023 Edition of American Recycler News
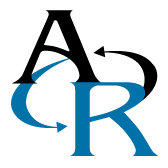