by MARY M. COX
Manufacturer List
|
Shears are an integral component in the process of construction and demolition. The Brokk® company offers the MC200 Multi Cutter to expand smaller Brokk models’ versatility for contractors in steel cutting applications. The product promotes safe and efficient steel material cutting in a variety of industries, including demolition, recycling, nuclear, process, food and construction. The steel cutting attachment, manufactured by Brokk’s sister company, Darda®, offers a high power-to-weight ratio and sleek, compact design. The attachment also addresses a need for a lightweight, economical steel cutting tool.
The 10” x 13” Multi Cutter is 40” long and can be used on machines weighing 2,650 to 6,170 lbs., including the Brokk 110, 120 D and 160 models. “This one-of-a-kind cutter brings easy maneuverability to confined jobsites with its slim profile, making it ideal for use in tight spaces, such as building interiors, where our machines excel, due to their electric operation and compact size,” noted Brokk vice president of sales and marketing, Peter Bigwood. The attachment also features a hydraulic 360° rotary drive for exact positioning and an 8” wide jaw opening, able to handle a variety of metals. It weighs only 265 lbs., yet uses a hydraulic booster to exert 50 tons of cutting force at 3,900 psi to easily cut through steel. To reduce costs to the end user, Darda also designed the MC200 Multi Cutter so operators can sharpen the jaws rather than replace them.
Bigwood added, “The MC200 Multi Cutter, combined with the smaller Brokk machines’ remote capabilities and arms that extend as far as 16’, allows contractors to easily cut beams, cable, supply lines and steel pipes in hard-to-reach areas. This improves efficiency and minimizes labor costs. Paired with a Brokk machine, the attachment reduces the risk of injury to laborers by eliminating the need to climb scaffolds and ladders with handheld tools. The Multi Cutter also alleviates the risk of injury from open-flame torches, which are a common but dangerous method for cutting steel. This traditional approach can also create fire hazards and increase the risk of exposure to harmful emissions.”
Indeco ISS Steel Shears have been specifically engineered to meet the demands of today’s scrap and recycling industries. “They are super tough and the culmination of over 35 years of hydraulic engineering and manufacturing experience. Our products make a job more manageable and so increase productivity – and they handle all types of steel demolition and scrap processing tasks. The ISS Series is available in a variety of mounting configurations including fixed, second member and rotating and third member,” Bill Pankracij, public relations director, explained.
The Indeco ISS Series models feature a special Hardox® main body frame, an integrated regeneration valve which accelerates no-load movement of the jaw and a pivot group that prevents the jaws from buckling. Pankracij noted, “The ISS cycle time is 30 percent faster than similar products on the market –due to the ISS integrated regeneration valve – and the Hardox steel eliminates shear flexing. Our exclusive oversize cylinder design can withstand over 10,000 psi of pressure, which is ample for any type of working condition. The shear’s quick change wear bushing ensures the knives are always optimally aligned and the continuous, high-speed 360° hydraulic rotation of the shear allows for better positioning and optimal cutting in any working position. Dual piercing design from both the upper and lower jaws improves cutting ability and the heavy duty pivot group provides long-term cutting efficiency.” He said four identical main knife blades are designed to be interchangeable and rotated three times to get maximum usage and cutting ability.
A patent is pending for the shear’s dual guide pack system, which can infinitely adjust alignment and prevent deflection in both directions during the cutting cycle. Special second and third member mounting bracket systems are available on all shear models and accessory options include blades and connecting hoses.
Kinshofer, one of the world’s leading sources of high quality excavator and loader crane attachments, offers the DXS Series of hydraulic mobile excavator shears, and the DXS-50 is the newest model. The line features Kinshofer’s DemaPower™ cylinder technology to give the DXS-50 the same power as shears two sizes larger. The cylinder uses 4 chambers instead of the 2 found in other shears, resulting in 20 percent more surface area within the cylinder. That allows the DXS Series to exert up to 25 percent more power from a smaller attachment, resulting in the best power-to-weight ratio in its size class. The 9,920 lb. DXS-50 features a 1,203 ton closing force.
The DXS-50 fits 25 to 35 ton carriers when boom-mounted and 32 to 50 ton carriers when stick mounted. Also, the cylinder technology allowed Kinshofer to design the DXS-50 with a jaw opening 29.2” wide and 30.7” deep.
“Our product’s double-acting speed valves and innovative cylinder technology also give the DXS-50 superior jaw closing and opening speeds. The cycle time is as fast as 5.5 seconds, 50 percent faster than any model in the attachment’s weight class,” Francois Martin, Kinshofer North America general manager, noted.
Martin said the DXS-50 reduces carrier fuel consumption by up to 20 percent compared to other shear models. The attachment’s efficient design allows it to function normally when the carrier is set in economy mode, achieving the same performance as a competitive shear on an excavator running at full throttle.
“The DXS-50’s high power-to-weight ratio and narrow frame make it ideal for top-down demolition, a technique growing in popularity in urban areas. Contractors can use smaller carriers to better reach areas to demolish, plus the attachment’s light weight and superior cylinder technology improve fuel efficiency while the excavator arm is fully extended. The DXS-50 complements Kinshofer’s demolition attachments, many of which also feature DemaPower cylinder technology for improved power, speed and productivity. We offer a wide product range with just about every type of attachment for equipment carriers with and without hydraulics in industries as diverse as scrap, demolition, railway, landscaping, construction, snow clearing, excavating, road building, forestry, tire recycling and biomass,” Martin concluded. The Kinshofer group of companies also includes Demarec, RF Systems, Auger Torque and Solesbee’s brands.
Rotar offers high quality concrete demolition tools that can separate steel and process concrete. “We focus on saving money for our clients, providing quality product performance, an environmentally friendly approach to design and leading the way in green sustainability manufacturing,” explained Sal LeCorte, national sales director.
The firm’s premier product is the mobile hydraulic steel processing shear, which is part of the RSS Series. “Our shear out-cuts and out-performs any similar product in production work. The custom designed, hydraulic speed-valve of the shear improves processing speed while saving carrier fuel usage. The RDC Series primary demolition tool leads the market in cutting performance and light weight design. Utilizing the latest steel composition wear abrasion steel technology, the RDC Series is built from Strenex 900, the latest in high performance tool steel.
“For material handling work, the high performing RG Rotational grapple is just the tool for your needs. Using a heavy duty high pressure cylinder, the RG grapple holds steady at any load amount and places it precisely where you want it. The dual-drive rotational system out performs any hydraulic rotational grapple in its class, whether for hurricane clean up or in handling waste material at transfer stations. Our RSP secondary concrete processor is a specialized tool. A fast cycle time and superior hydraulic cylinder force allows the RSP to make quick work of any production concrete job. At a lower than average cost than similar products, it is the exact tool needed to make money for you,” said LeCorte.
Folks at Rotar have built high quality equipment for the demolition and steel scrap processing industry since 1978. Their products are built in Holland and sales and distribution facilities are located worldwide.
Published in the February 2018 Edition
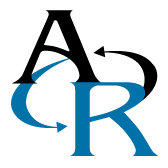