
ManufacturerBCA Industries
John Neuens
414-353-1002
www.bca-industries.com
CM Shredders
Mario Vazquez
800-848-1071
www.cmshredders.com
Deltax International
Shelly Zelunka
800-268-6797
www.genscoequip.com
Eagle International
Anthony Yarger
800-755-8473
www.eagle-equipment.com
Ecoverse Industries
Dan Delciappo
440-937-3225
wwwecoverse.net
Eldan Recycling
Carsten Nielsen
716-731-4900
www.eldan-recycling.com
Franklin Miller, Inc.
Ed Gajewski
973-535-9200
www.franklinmiller.com
Gradeall International Ltd
Stephen Murphy
44 28 8774 0484
www.gradeall.com
Granutech-Saturn Systems, Inc.
Greg Wright
877-582-7800
www.granutech.com
M&J Recycling
Keith Ely
857-276-7994
www.mjrecycling.com
SEDA Environmental LLC
Bruce Henderson
770-681-0474
www.seda-usa.com
SSI Shredding Systems, Inc.
Lee Sage
800-537-4733
www.ssiworld.com
Untha America
Julia Reichenbach
603-601-2304
www.untha-america.com
|
According to Business Research Insights, the global rubber recycling market will reach the $4,658.91 million mark by 2031. Through recycling, scrap rubber can be converted to pyrolysis oil, tire-derived fuel, and many other rubber products for a variety of markets. The equipment offered by the following companies below can be used for rubber and tire recycling.
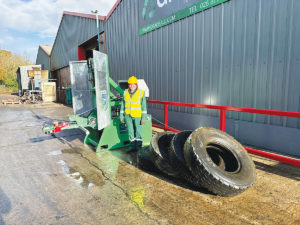
Gradeall International Ltd
The DTX 4/600 Alligator Shear available from GENSCO, is a heavy-duty shear suitable for tire and scrap metal processing. “Engineered for durability and efficiency, this alligator shear sets a high standard for efficient processing of tires and other scrap material that requires up to 24” blades and a wide jaw opening,” With multi-tier quality inspections for every shear that leaves the warehouse, and a lifetime of tech support, GENSCO offers the highest standard of recycling equipment, stated Shelly Zelunka.
Zelunka added, “The DTX 4/600 is standard with foot-pedal control and 4-sided blades that are reversible, regrindable and that ensure sustained cutting performance. With a strong cutting force of approximately 120 tons in the throat, the shear effortlessly handles challenging materials, making quick work of tire beads and scrap materials. Equipped with an adjustable jaw opening, the DTX 4/600 easily adjusts to various tire sizes and reduces cycle time for smaller tires. This adaptability is important, especially when efficiency is a priority.”
Designed for continuous use, the DTX series has been a staple in scrap processing operations globally. Since 1919, GENSCO has been at the forefront of supplying a full range of equipment to the recycling industry. The DTX 4/600 offers decades of know-how, reliability and the flexibility required by heavy duty scrap recycling operations. It exemplifies GENSCO’s expertise in handling high-tensile metals, including those found in tire beads. Alligator shears from GENSCO range from bench-top models to 40”-blade models, designed for rail and structural steel cutting.
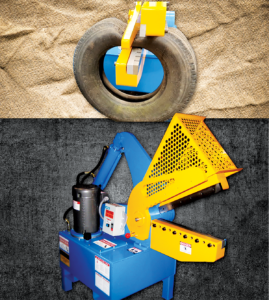
Deltax International
Gradeall’s truck and agricultural tire sidewall cutter is designed to process semi-truck tires and more as the machine effectively removes the sidewall, which contains the thick steel bead inside each tire. This technique eliminates the shape memory effect, leaving a relatively flexible tread section and two sidewalls, which simplifies storage, transportation, shredding, and recycling processes related to scrap tires. “Our compact sidewall cutter is simple to use, safe to operate, and easily maneuvers, on-site. Recommended usage conditions include level concrete surface placement and a 415v, 3-phase power supply, and the tool steel blades are durable and efficient,” Stephen Murphy, Managing Director, said.
“In areas where whole tire transporting is prohibited, this machine also offers an ideal solution. With an optional tread cutter attachment, the side-wall cutter can be used to further process tread sections into smaller, manageable segments, which is particularly useful for cumbersome tractor tires. This option also typifies Gradeall’s holistic approach to tire recycling, since downsized material is more easily transported to shredding facilities, and pyrolysis plants and can be further processed by a conventional baler. The Gradeall MK2 tire baler produces a PAS108 standard tire bale,” Murphy noted.
He also explained how “a unique, valuable application for truck scrap tire sidewalls is their use as silage pit covers, vs. auto scrap tire use. Truck tire sidewalls are almost as heavy as car tires, but have a larger footprint, lie flat and so don’t hold water. Auto scrap tires are commonly problematic as they retain water, which stagnates and the resulting rancid, green liquid is unpleasant to handle. Also, during the off-season, car tires are typically stored in a pile. When not in use, flattened truck tire sidewalls can be easily managed using a Gradeall storage product.”
Gradeall is a manufacturer of waste handling and recycling equipment with over 30 years of experience, supplying a diverse range of industries that require waste management solutions. Based in Northern Ireland and specializing in the design and manufacture of processing equipment for scrap tires of all sizes, Gradeall is a significant, global player in this sector.
According to Greg Wright, vice president of Granutech-Saturn Systems, “Tire recycling is a large segment of our business and we manufacture equipment for all stages of tire recycling – from the primary shredder to fine grind refiner mills and everything in between. Tire Derived Fuel is still a large segment of scrap tires and many other segments continue to grow, including rubberized asphalt, sports turf crumb, and rubber mulch. The science behind pyrolysis continues to advance as well.”
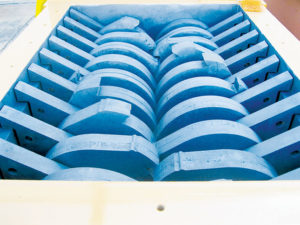
Granutech-Saturn Systems, Inc.
Granutech offers over 50 years of manufacturing experience in size-reduction equipment. Added Wright, “The equipment we manufacture and recommend for tire recycling can vary greatly, depending on the customer’s requirements. Depending on the final product size required, processing rates can range anywhere from one ton per hour up to 20 tons per hour. If a customer only wants to make a primary shred or a chip, we would recommend one of our dual shaft shredders, possibly with an external sizing screen, or a quad shaft shredder. If the goal is to reduce tires to a powder, then four stages of processing with various pieces of equipment at each stage are involved, performing various tasks. Reducing tires to crumb rubber is much different than performing a primary shred or chip, as removing the steel and fiber becomes a large part of the process, at different stages and with a variety of equipment.”
Published in the February 2024 Edition of American Recycler News
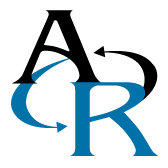