by MARY M. COX
Manufacturer List
|
According to an IBISWorld report published in August of last year, the U.S. electronic goods market is $8 billion in size, employs over 34,000 people and involves over 2,600 businesses. Further expansion is projected as regulations and volumes continue to rise, relative to the materials involved.
The items collected and sorted in this industry include televisions, mobile telephones, tablets, computers and various similar items. Naturally, there are companies that manufacture equipment that can be used to process this specific waste stream. Conveyors are just one of the components that may be used in any given recycling operation for electronic refuse.
DeHart Recycling Equipment has manufactured a variety of conveyors for several decades for customers across the nation. “Until a few years ago, almost all of the conveyors manufactured by DeHart were designed for applications related to traditional recycling, however, in recent years there has been increased interest in electronics recycling among our customers. As a result, we provide customers with equipment systems to recover the valuable materials found in discarded electronics. These systems typically include a number of conveyors that interface with container dumpers, sort platforms, shredders, optical sorters, and magnetic separators. E-waste is comprised of many different materials, so in these applications it is key to have efficient separation of materials. DeHart designs and manufactures conveyors in-house to provide customers with a tailor-made solution to their electronics recycling needs,” stated John Greider, Jr., regional sales manager.
As the popularity of electronics recycling continues to grow, Greider expects to see a correlating increase in demand for that type of recycling equipment, particularly shredders and conveyors. “We have already seen an increase in the number of inquiries from those starting an electronics recycling operation and certainly the volume of e-waste seems to be increasing as well. The process of separating and recovering the variety of materials found in electronics tends to necessitate more conveyors than you might need to recycle OCC, UBC, etc. For a customer to efficiently recycle electronics the person needs an infeed conveyor to a shredder, followed by a discharge conveyor to bring the material to sort. A variety of conveyors can be used in the sorting process. For a manual sort line there is typically a variable speed conveyor on a platform, linked with several stations where sorters are located. For customers that use a mechanical sorting device, we can build a conveyor that allows the optical sorter/ballistic sorter/magnetic separator to perform at its best,” Greider explained.
Hustler Conveyor Company designs, manufactures, and provides complete solutions for sorting and separating electronic scrap. “As an industry leader for more than 50 years, we ensure that safety and reliability are always a top priority when it comes to engineering and constructing our equipment. We design all of our equipment to be as dependable as possible to reduce down time, and maintenance cost,” explained Cody Gonzales, sales associate.
“We offer a wide selection of heavy duty conveying and separation equipment for handling electronic scrap. Our conveying equipment includes steel belt, roller chain combo belt, and a variety of flat belt and oscillating conveyors. An assortment of separation equipment that includes cross belt magnets, drum magnets, eddy current separators, and sensor sorters is also available. We can supply individual components or design and furnish a complete system. A typical system would include a steel/roller chain belt in-feed conveyor, which would feed the required size reduction equipment (shredder). The shredder discharges onto an oscillating conveyor that can be supplied with a screen section to remove any fine or small material. Material would then be conveyed to the separation equipment which would consist of magnetic separators, eddy current separators, and sensor sorters, by using various types of conveyors. We custom design all of our conveyors to any required width and length to meet the required system throughput,” stated Gonzales.
He noted that efficient material recovery and obtaining a pure end product are some of the chief concerns when recycling electronics. Gonzales concluded, “We supply our customers with equipment that will provide optimum separation, and increased material recovery. This results in a higher quality of material. We’re able to do this by engineering our conveyors and separating equipment so that our products include the flexibility to adjust and accommodate various material mixes.”
According to General Operations Manager, Jeff Sayre, “Tuffman® incline conveyors are ideal for processing electronic waste, whether as add-ons to sorting systems or for feeding material into trommel screens or other sorting devices. The Tuffman-Eriez® metal separation system offers a complete solution for e-waste sorting and separation. Complete with several Tuffman incline conveyors, the metal separation system effectively separates ferrous and nonferrous metals from waste.” Tuffman is a division of Worldwide Recycling Equipment Sales.
Sayre said Tuffman conveyors are used in a variety of material recovery projects, including electronic waste. Their 32’ heavy-duty incline conveyor is used for feeding material into a trommel screen or from the trommel screen to the sorting station. The 12’ portable incline conveyor is a shorter, mobile conveyor that can be easily moved from location to location, making it convenient for smaller transporting jobs around a site. Powered by a 20 hp, 3-phase electric motor, the Tuffman 532ED extreme duty conveyor is the firm’s largest, most durable conveyor. It is best-suited for transporting more taxing material, such as computer monitors, circuit boards, and other electronic waste.
“Tuffman Equipment is a proven leader in the waste processing and material recovery industries. We specialize in the manufacture of material recovery equipment, including sorting stations, trommel screens, crossbelt magnets and conveyors. We can also custom-design and manufacture to order,” Sayer said
Published in the July 2015 Edition of American Recycler News
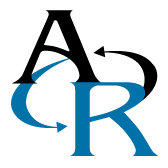