by MARY M. COX
Manufacturer List
|
Concrete is typically a ubiquitous material in construction and demolition settings. Concrete is heavy to handle and to transport. If sent to a landfill, concrete can further add to processing costs. Recovery and processing of the material can be aided though the use of concrete crushers.
For nearly 30 years, the IROCK Crushers Company has manufactured mobile and portable crushing and screening plants, conveying equipment and other related products for the demolition, recycling, and aggregate industries. Products are designed and manufactured with both dealer and end user in mind, with a focus on the contractor and recycling market.
“Our robust equipment increases production and profits while also reducing downtime and operational expenses. In addition to a premier product line that is easy to service and operate, IROCK provides expertise and outstanding service and support from a staff of industry experts,” Fred Gross, sales and development director, stated. The IROCK warehouse is stocked with wear and replacement parts, readily available to support dealers and end users. The firm’s after-market sales and service team provides round-the-clock and weekend availability, to support any emergency.
Producers and contractors frequently face the challenge of downtime and lost profits – a result of lengthy setup and takedown times on units. “Unlike most plants, IROCK’s hydraulic setup functions allow the machine to be set up and ready to operate in minutes. This provides a producer with maximum production time and the ultimate user-friendly experience. Our TC-15CC horizontal impact crusher is the ultimate processing machine for the recycling market. The machine’s 37 x 43” inlet opening is the largest in its class. Designed primarily for the small to medium sized contractor, the crusher easily handles C&D recycling challenges with materials such as concrete, asphalt and bricks. Also, it can be operated in the most demanding recycling applications and with extreme efficiency with pre-screen, under crusher pan feeder and cross-belt magnet operations. The return conveyor can also articulate out perpendicular to the machine, to stockpile oversize and midgrade product,” concluded Gross.
Kinshofer, a manufacturer of high quality excavator and loader crane attachments, manufactures the WS Drum Cutter Series of products. The drum cutters feature an exclusive pick angle and optimal chisel arrangement for high performance and minimal wear, making the attachments ideal for many industries, including demolition. Francois Martin is North America general manager at the company and he said, “Years of engineering and manufacturing have shaped the WS-Series Drum Cutters into precise rock breaking units that maximize efficiency and outperform the competition. Application specialists work with contractors to choose the best drum and chisel for their specific application, minimizing noise and vibration while optimizing performance. Drum cutters are a quieter alternative to hydraulic breakers and the WS-Series of products are some of the quietest in the industry, making them excellent for use in areas with noise restrictions. They also produce less vibration than breakers, so contractors can use them where there’s a risk of disturbing a nearby structure’s foundation.”
Martin reports that Kinshofer has a drum to match any application. The rock drum effectively breaks soft to medium-hard rock in with its strategic chisel pattern while the profiling drum’s higher density of chisel shapes and levels soft to medium-hard rock in other applications. The demolition drum offers reduced vibrations due to a wear-protected spiral sheet and is ideal for cutting medium-hard to hard rock as well as concrete.
Selecting the proper chisel and drum combination is key to optimizing performance and reducing attachment wear. Kinshofer’s application specialists work closely with customers to understand applications and material conditions so they can recommend the best drum and chisel tip for each situation. WS-Series Drum Cutters are available in 7 models for 2 to 60 ton excavators. For added versatility, the attachment can be paired with Kinshofer’s NOX Tiltrotator, which enables 360° continuous rotation and multi-directional tilting up to 55°.
Metso manufactures the Lokotrack® LT1213 and LT1213S mobile crushing and screening plants for recycling applications. The Lokotrack LT1213S is a fully equipped mobile impactor plant with a high capacity, dual-slope screen and return conveyor. The LT1213 has the same features and options without the screen or return conveyor. Both plants can be docked in a few minutes and fine-tuned for top soil, concrete, asphalt, and demolition waste recycling applications with features like vibrating grizzly or pan feeder under the crusher.
“The LT1213 and LT1213S are built around the powerful Caterpillar® C13 diesel engine and Metso’s dependable NP1213M impact crusher. The plants are designed to operate together with other Lokotrack mobile crushing and screening models and can be transported as a single unit on a low-bed trailer. Our advanced gearbox comes standard for either machine. The gearbox provides the most efficient crusher drive system on the market with assisted start and brake. Optimized hydraulic circuit with independent fan and stand-by function reduces noise when idling and saves up to 20 percent on fuel consumption, meaning more power for the crusher. A hydraulic radial return conveyor also makes the LT1213S easy to operate in closed and open circuits. Crusher service rotation is done by 24V hydraulic power pack. Easy-to-use tools are provided to help change blow bars and breaker plates,” explained Ben Hansbury, vice president, distribution sales.
Published in the July 2019 Edition
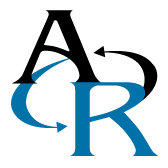