by MARY M. COX
Reducing material size for more efficient handling is a common concern in the recycling industry.
Manufacturer List
|
When plastic is the material involved, there are a wide range of products available to recyclers for processing it.
Cumberland offers products to reclaim material from the following: bulk reclamation of post-user industrial and consumer scrap, standard manufacturing or off-spec and malformed or bad product from manufacturing. The firm’s granulators are for recycling, injection molding, extrusion, blow molding and all other polymer industry processes. Their beside-the-press product array ranges from small (6 x 8”) units to large (16 x 40”). Mid-size units include the T500 series, available in 3 sizes, 5070 (20 x 28”), 5090 (20 x 36”) and 50120 (20 x 48”).
Their central-type granulator line is for large part, heavy construction, or high volume requirements. All products are available with sound suppression, are UL-compliant and meet or exceed every OSHA and international standard.
According to John Farney, national sales manager, “Market conditions are good, but indicators for the remainder of the year rely on continued advancement in the consumer goods and automotive areas. Building material markets show promise for the balance of 2014, and for the fourth year in a row, projections are good for general market growth. The demand for state-of-the-art products, high quality, minimal maintenance units, and highest possible productivity continue to drive product development.
“We strive to provide products that are useable with minimal setup time as stand-alone products. Integrated systems, of course, require assembly and integration, but standard products require minimal set-up time. We are celebrating Cumberland’s 75th anniversary, and dedication to our industry, our clients and our environment continue to steer our efforts.”
Herbold Meckesheim USA, a subsidiary of Herbold Meckesheim Germany, sells and installs durable, high-quality size-reduction equipment (granulators, shredders, grinders, pulverizers, etc.) and wash-line systems for recycling all kinds of industrial and post-consumer plastics. “Units are designed as modular ‘building blocks’ so that a system can be extended or modified according to the customer’s requirements,” said David Lefrancois, president.
Last fall, Herbold introduced five models of the HOS Heavy-Duty Pipe Shredder, which efficiently (up to approximately 3,400 lbs. per hour) reduces large (to 0.8’ in diameter), thick-walled plastic pipes to chips of approximately 2.5 to 4 sq.in.
Lefrancois said, “Herbold’s extensive line of granulators includes heavy-duty, general-use and compact machines. Popular HB and SB Series horizontal models employ a hydraulic ram or screw-feed mechanism, which makes them quieter and more efficient (30 to 50 percent higher throughput) than same-size gravity-fed cutting chambers. Suitable for dry or wet operation, these granulators are capable of processing up to eight tons of plastic per hour.
“The blade geometry of Herbold granulators, in combination with an open rotor, provides for cleaner cuts, higher capacity, fewer fines and less noise. The knives can be removed easily and safely, and adjusted precisely in a fixture outside the unit. Our knives also last longer because their design provides 18 millimeters of regrind capacity, nearly twice that of most competing models.”
Lafrancois explained that another benefit of Herbold horizontal granulators is a diagonally split housing that allows complete access to the cutting chamber for faster maintenance. Rotor bearings are positioned outside the cutting chamber, to keep grease from contaminating product.
He said the trend toward recycling and sustainability is still on the upswing, so “Herbold Meckesheim’s future appears bright. Thanks to recent advances in automated separation equipment, more receivers of recycled plastics are separating the waste stream by material type, for single-line recycling systems. This makes it easier for generators of plastic waste to recycle, and consequently makes it more likely that they will.”
For over 30 years, Rotogran International has designed and manufactured size reduction equipment for recyclers and plastic processors. Mike Cyr, president, stated, “We are a true North American manufacturer of granulators, conveyors and evacuation systems, building everything in-house with spare parts readily available on our shelves. For the recycling industry, Rotogran produces severe duty, high-production granulators with rates up to 10,000 lbs. per hour, specifically designed to operate 24/7 at maximum capacity.
“Our Titan series of recycling granulators are the workhorse of the industry, featuring huge, 36” diameter cutting circles, combined with .5” thick screens, creating a massive, high-yield screen open area. Severe-duty rotor construction features a 12” diameter main shaft and solid knife support blocks across the entire chamber width, ensuring structural integrity. Available knife configurations range from 3 to 13 rows. The rotor is driven with twin solid steel flywheels, weighing over 2.5 tons through a TEFC premium efficiency motor. Our cutting chamber is fabricated using 3” thick plates and welded construction with easily replaceable wear inserts in key areas to protect your initial investment. Easy access for blade changes and routine maintenance is achieved with hydraulic cylinders driven by an independent, self-contained hydraulic power pack.”
Cyr also said that Rotogran recognizes and acknowledges a new trend in the recycling industry toward sophistication, process improvement and expansion, combined with upgraded safety measures and protection of invested equipment.
“Some of these trends appear in the form of more advanced, high end metal detectors to produce products with zero metal contamination and increased resale value. These advanced metal detectors are used between pre-shredding equipment and granulation equipment to improve granulator performance, reduce maintenance intervals, maximize blade life and improve overall profit by producing the cleanest, highest quality regrind possible. These equipment combinations are often integrated into systems with advanced control panels. These controls adjust the system on the fly for maximum production and to maintain the highest level of safety for the operators and support personnel around them,” he noted.
Cyr believes that today’s recyclers are at the top of their game and expanding into further processing capacities “and Rotogran is with them every step of the way,” he concluded.
Published in the June 2014 Edition of American Recycler News
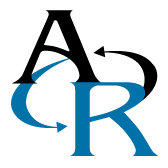