Manufacturer List
Mike Wilks 316-284-2020 www.buntingmagnetics.com Eriez Magnetics Gensco America, Inc. Magnetech Industrial Services, Inc. Magnetic Products, Inc. Moley Magnetics, Inc. Ohio Magnetics Inc. SGM Magnetics Corp. Winkle Industries |
Due to the increasing demand for steel and the urbanization and industrialization in developing countries, the metal recycling market is projected to be $76.1 billion by 2025 (Markets & Markets). As those in the industry seek to cull the maximum yield from their scrap metal stock, magnets are often one of the tool types used in that effort. Methods and products vary and of course, it is important to confirm the best type of tool for the material configuration involved.
Bunting’s patented stainless steel separation conveyor (SSSC) allows for recovery of up to 98 percent of small and mid-fraction 300 series stainless steel and up to 94 percent of large fraction stainless steel from ASR zurik lines. A magnetic circuit design of high int
ensity neodymium magnets maximizes stainless steel recovery and removal in applications such as general recycling, auto shredding and wire chopping streams. The SSSC provides maximum removal of stainless steel and ferrous dust from wire fraction and the purest zurik, maximizing scrap metal recovery profitability.
“The SSSC is the only product available in the modern recycling market that achieves such high stainless steel recovery levels. Bunting’s on-site testing facilities allow our clients to see how their material interacts with the SSSC in real time, and provides valuable performance information. We offer extensive custom design options because our engineers work with our customers to identify and deliver the most effective equipment solution for their operations,” said Mike Wilks, global marketing director.
He added, “With multiple SSSC features designed to maximize separation efficiency and streamline operations, the machine is equipped with 8” and 12” diameter patented, high intensity neo magnetic circuit head pulleys, capable of holding all sizes of 300 series stainless steel. Also, the product’s VFD controllers, operating between 30 and 120 fpm, deliver effective separation and general capacities run about 1,000 lb./hr./ft. width on small fraction, 1,500 lb./hr./ft. on mid-fraction, and 2,000 lb./hr./ft. on large fraction. SSSC optional features include a patented air knife, discharge hood, and vibratory feeder. Generally, product recycling purity directly correlates to profitability and higher purity product results in greater profit. Product that is excessively contaminated can sometimes result in no profit at all. Call Bunting today, and we can help you maximize your scrap purity and profitability.”
According to Alan Zelunka, owner of Gensco Equipment, “Gensco magnets of all sizes and capacities, designed for the roughest of applications, are proven in use every single day. Our magnets are built with cast steel shells, for long life and reliability. Deep field aluminum –and yes, some copper coils, are suitable for 230 volt DC operation in harsh scrap environments. Light duty versions are available for railway and demolition applications, operating on 24 volts DC. Gensco has lead the market by offering the first-of-its-kind Dynaset line of hydraulic-driven power and control systems, for use with mobile hydraulic machines. The original HMAG, built in a hydraulic-driven generator form, is suitable for countless applications.”
In addition to manufacturing magnets, Gensco has earned a reputation in the industry for a range of high quality products for scrap handling and processing. Included are scrap handling grapples, shears of all types and sizes, balers and briquetters, shredders and full systems for processing (cutting, stripping, chopping) scrap electric cables. “We’ve been part of the scrap industry for over 100 years and a major part of our success has been in the supply of thousands of circular scrap magnets to recyclers, mills and foundries throughout North America. We offer complete manufacturing and rebuilding facilities, parts, accessories and we serve the global market from locations in Toronto, Canada and Decatur, Georgia,” added Zelunka.
Brand manager Mark Volansky explained how the seasoned engineers and manufacturing team at Winkle deliver efficient and durable solutions in their lifting magnets, power and electrical control systems, to guarantee optimum performance for scrap metal recyclers. “Our industry leading OptiMag DS Series magnets are a proven choice for increasing productivity when lifting all types of ferrous scrap metal. Engineered with deep and extra-deep field wound coils, robust mechanical constructions and continuous duty cycles, the design features of this series ensure optimum performance without sacrificing durability. To utilize the full capacity of your crane, choose from Winkle’s diversified portfolio of circular scrap magnets, to improve throughput and maximize profitability.”
Volansky noted that Winkle’s DB Series magnets incorporate extra-heavy duty mechanical construction and extra-deep-field coils, to gain exceptional saturation levels, superior duty cycles and extended service life, without sacrificing service life and lifting performance. Their DSG Series grapple magnets allow operators to combine the tines of a standard orange peel grapple with the capacity of a round lifting magnet. Following magnet clean-up of an area, use the grapple to increase lifting capacity and hold scrap while de-energizing the magnet, thus saving on magnet wear and tear. Safely sort out valuable ferrous steel without changing to another attachment, and reduce labor costs while increasing return on ferrous metal. Unlike round magnets, DSR Series magnets are well-suited for loading and unloading rail cars, easily accessing corners and for complete clean out. This series can also be custom-designed, to maximize crane capacity. For work environment clean-up, Winkle’s RS Series magnets are a fast, efficient and practical solution to rid roadways of metal that cause costly tire and equipment damage. The rectangular magnets can be used with all types of machines –fork lifts to trucks – to eliminate metal from roadways.
“Our power supply product line –generators, controllers and more – along with our parts distribution and field service proficiencies, will all keep your recycling facility operating safely and effectively. The scrap industry continues to remain strong and it is important for recyclers to work with a company that can provide effective solutions, not just sell products to you. We sell and repair magnets and magnet systems for every application, but more importantly, we provide solutions to ensure the greatest success of our customers. Since 1949, Winkle offers tremendous experience in all phases of magnet and power system design, engineering, manufacturing techniques and customer service. This allows Winkle to offer complete service for every phase of metals recycling,” Volansky said.
Published in the March 2022 Edition of American Recycler News
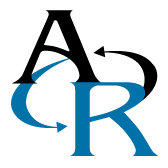