ManufacturerAlban NDE Flynn Spears 425-251-1986 www.albannde.com Bunting Tony Rampino 316-284-2020 www.buntingmagnetics.com Dings Company Magnetic Group Steve Tanzilo 414-672-7830 www.dingsmagnets.com Ecohog Ltd. Declan McNally 844-212-9200 www.ecohog.com Eriez Manufacturing Co. Mike Shattuck 888-300-3743 www.eriez.com IMRO Maschinenbau GmbH Adam Floyd 678-873-1973 www.imro-machinenbau.de Magnapower Equipment Ltd. Rustin Ross 847-480-8900 www.alanross.biz Magnetic Products, Inc. Kyle Rhodes 248-887-5600 www.mpimagnet.com Orbcon Adam Floyd 678-873-1973 www.orbcon.com SGM Magnetics Julie Most 941-342-8800 www.sgmmagnetics.com Steinert US Robert Broughton 800-595-4014 www.steinertus.com |
Eddy current separation (ECS), a process used throughout the scrap recycling industry, sorts nonferrous metals from nonmetallic material. The process is based on the principle that a time-varying magnetic field will induce electrical current to flow throughout a conductive particle. This current then reacts to the applied magnetic field, exhibiting a pronounced force of deflection and the material is efficiently separated and the result can even be environmentally beneficial. Various ECS designs have been used through the years but a belt-driven, rotary drum variety is one of the common methods used.
Dings Co. Magnetic Group has custom built eddy current separators, magnetic drums, self-cleaning overhead magnetic separators and other magnetic solutions for the recycling industry for 125 years. “When it comes to nonferrous metal recovery such as aluminum, copper and brass, we have eddy current models engineered for every process,” said Steve Tanzilo, magnetic group sales manager.
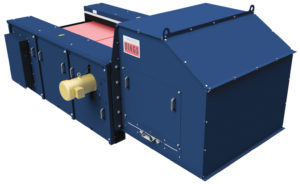
Dings Company Magnetic Group
He described how as a piece of nonferrous metal such as aluminum passes over an ECS, the magnets inside the rotor rotate past the aluminum at a high speed, forming eddy currents in the aluminum and creating a magnetic field. The polarity of that magnetic field is the same as the rotating magnet, causing the aluminum to be repelled away from the magnet. This repulsion makes the trajectory of the aluminum greater than that of the nonmetallic material, allowing the two material streams to be separated.
“Our ECS products are available in concentric and eccentric versions. Dings’ concentric ECS is ideal for recovering aluminum cans and other, larger, nonferrous metals. Our eccentric eddy current models are specifically engineered to remove fractional sized, nonferrous metal from mixed material streams. The concentric design involves a triple shell layer of ceramic tile, fiberglass, and a heavy duty stainless steel shell that protects the rotor assembly and reduces maintenance and replacement costs. The machine is manufactured with a heavy duty, structural steel I-beam frame and support structure, oversized shafts and bearings, and a heavy-duty drive package,” Tanzilo stated. He continued, “The eccentric model design concentrates the magnetic field, which releases ferrous materials sooner in the process. It is engineered with Dings’ double shell layer design, which provides maximum protection of the rotor assembly. This design also significantly reduces overall maintenance and replacement costs of the ECS. Both versions of our ECS have a removable access panel, making maintenance and removal of the polyurethane or nitrile wear-resistant belt, easier and faster.”
Adam Floyd, process and business development director of Orbcon, noted that “Eddy current separators are one of the most efficient recycling tools to maximize profits and yield very fast ROIs. They are able to process high volumes and separate even the finest nonferrous metals. IMRO has been the home of eddy currents for over 30 years with thousands of eddy currents shipped all over the world from our manufacturing facility in Germany and U.S. Orbcon distribution centers. With a 44 pole high frequency and an up to 100’’ width, the IMRO RCSX F-240 Condor eddy current can recover nonferrous metals of even 0.5 mm. This ECS spins at 3,800 rpm and is equipped with a patented horizontally and vertically adjustable electrical divider with memory function.”
Floyd claims that a key ECS element for effective separation of nonferrous metals is the proper sizing of the material to be processed, prior to ECS use. If the material to be processed is narrowly sized, it greatly improves ECS performance. As a rule of thumb, it is important to maintain a 3:1 size ratio (or smaller) between particles. If this ratio increases to 4:1, the recovery or quality of the nonferrous metals could be impacted.
He cited some other important factors to consider when procuring an ECS: belt thickness, magnetic strength and frequency. “With the proprietary technology within IMRO products, we are able to address these three key variables to significantly increase metal recovery and product quality when compared to our competitors.” Floyd added, “By designing two new types of eddy currents, IMRO offers a unique purifying system, which is a solution to the biggest industry challenge: achieving the highest possible metal recovery and purity levels.
Proper maintenance is important for ECS longevity, Floyd also said. A typical ECS life span is about 15 years when properly maintained. IMRO recommends that at the 12 to 15 year mark, checking the Gauss reading on the pole drum of a machine, to confirm the strength of the magnetic circuits. Exposure to high and seasonal fluctuating temperatures over time can affect the strength of the magnetic fields of an ECS.
Floyd stated how “Eddy currents contribute greatly to the reduction of CO2 emissions, through the replacement of primary metal ore resources. A given carbon footprint can be reduced by up to 90 percent if aluminum is separated, recovered and recycled via an ECS. The use of an IMRO ECS can greatly benefit MRF, RDF, e-scrap, IBA, ASR, metallurgical slag and wood processing operations, glass, plastic and textile recycling operations.”
STEINERT is a leader in sensor sorting and magnetic separation, and claims the ECS they manufacture is an efficient, effective solution for separating metals. “Recovering nonferrous metals – those that contain aluminum, copper, zinc or brass – is the economic basis of countless recycling systems. Our separators, with an eccentric pole system, provide optimal recovery of those metals,” said Robert Broughton, president of STEINERT. It is no coincidence that more than 4,000 of them are in use worldwide; thanks to the high extraction volumes and the durability they offer.”
A STEINERT ECS produces a mixture of nonferrous metals, derived from different sorting materials. As the market favors pure metal fractions, for most customers, additional sorting steps are required to extract, for example, pure aluminum from a nonferrous metal mix. STEINERT’s XSS® T EVO 5.0 x-ray sorting system helps to solve this challenging task by detecting material-dependent differences in the absorption of x-rays and then classifies and uses them for sorting into density classes.
“Eddy current separators recover nonferrous metals from end-of-life vehicles, e-waste, incineration bottom ash, and other post-consumer scrap,” Broughton said. “STEINERT achieves extraordinary separation results through the use of neodymium-iron-boron magnets, a thin conveyor belt, and an electrically non-conducting drum shell made of composite fiber materials. These ensure maximum field strengths and, thus, precise, efficient sorting – a technology that plays an important role in preserving resources. Our products help keep increasingly scarce resources in circulation. Together, we work with our customers to build a circular economy to ensure the world won’t run out of resources.”
Dating back more than 130 years, STEINERT’s family-owned business is based in Germany. The firm offers some of the world’s leading experts in sensor sorting and magnetic separation for waste and metal recycling as well as mining. With subsidiaries in Germany, Australia, Brazil and the U.S., the company also has 50 sales partnerships and joint ventures across the globe.
Published in the March 2024 Edition of American Recycler News
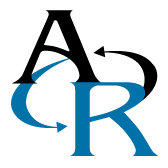