Manufacturer ListDave Packer 800-803-3365 www.aimattachments.com Anvil Attachments LLC Bateman Manufacturing Bodine Manufacturing Builtrite Manufacturing LLC Fuchs Iron Ax, Inc. Kenco Corp. Kinshofer USA Moley Magnetics Inc. Pemberton Inc. SAS of Luxemburg LLC ShearCore Young Corporation |
In the auto and scrap recycling industries, a large variety of attachment products are needed to handle the variety of materials that are recovered and further processed. Shears, crushers, buckets and magnets are just a few examples of the items commonly used by machine operators.
Bateman Manufacturing has provided scrap handling solutions to their customers for decades via products such as orange peel grapples, mag-grabs and the ships gear grapple. The company offers grapples in varying sizes to fit the needs of the scrap industry. “Whether you need a 1 yard grapple or a 13 yard, we offer the most diverse scrap grapples on the market. Our orange peel grapple has become a staple for auto recycling. The ease of use and durability of this product are two of the most common reasons why our customers continue to choose Bateman over other manufacturers,” commented Mark Vandenburg, general manager.
Bateman has experienced significant growth in the last few years due to the high demand for their products. In order to meet the needs of their customers, Bateman has made broad improvements to streamline production rate and to ensure quick lead times. “We’ve made strides this year because our production volume increased significantly, compared to last year. Along with Bateman products for scrap applications, we manufacture a range of other attachments, vital to other industry sectors as well. Whether it’s a clamshell bucket for port use, a wood rake power grapple for forestry, contractor grapples for demolition, or rail grapples for railway settings, we can provide the equipment needed to help get the job done. We’re proud to offer our 30+ years of experience in manufacturing high quality products to our customers – in whichever industry may be involved,” Vandenburg concluded.
SAS products are designed to meet the needs of high volume; high production auto processing facilities and their product line of wheel loader forks and auto processing equipment “will get the job done faster and easier. SAS employees strive to design and manufacture the most cutting-edge, highly durable attachments with every product supplied to the market and we work diligently to advance the process of saving time and increasing profits throughout the industry,” stated Adam Lindley, president.
Lindley added, “Our Extreme Auto Processor continues to provide performance that stands at the forefront of the market. Best suited for excavators weighing 16 to 31 metric tonnes, the product allows customers to extract ferrous as well as valuable nonferrous materials, garnering extra revenue from every vehicle. As many continue to manage a labor force deficit, this product allows an operator to do the job of several people, which helps decrease costs and helps to eliminate injuries from sharp metal and broken glass when manually removing wire. As scrap prices fluctuate, processing vehicles thoroughly will increase revenue across the board and allow customers to maintain volume throughout their facility.”
Evolving from an auto salvage yard in the early 70s, SAS developed the first long car handling forks, which marked the birth of the company. Now, SAS is celebrating 50 years of business, manufacturing engineered tough attachments, which supply solutions to the auto salvage and scrap metal industries, for severe duty applications.
ShearCore has experienced incredible growth in the scrap, recycling and demolition industries. The firm’s FS Mobile Shear series includes eight models – FS25 (5,900 lbs.), FS35 (7,200 lbs.), FS45 (11,200 lbs.), FS 55 (13,000 lbs.), FS75 (15,700 lbs.), FS85 (17,900 lbs.), FS 95 (21,600 lbs.), FS145 (29,200 lbs.). All model weights are listed as rotating shears and non-rotating models are available in FS45-FS145. “The Fortress Mobile Shears are designed and manufactured to cut more, last longer, and are easier to maintain. Our shears are purpose-built for scrap metal processing, demolition, and demolition/reconstruction. Our unique machining capabilities allow us to utilize a 6” high-yield plate and use few overall components. Fewer components mean fewer welds for a structurally superior shear. The shear has a two-piece piercing tip with a zipper seam and dowel pins, along with a longer razor blade that sits outside of the guide blades,” explained Jay McDevitt, sales director.
Shear Core’s FC Demolition Shear (concrete processor) series offers 3 models – FC25 (6,000 lbs.), FC35 (8,100 lbs.), FC45 (10,000 lbs.). Weights may vary, depending on configuration options and listed weights are typical flat top, so with no bracket. The Fortress Demolition Shear is purpose-built for crushing and processing concrete in both primary and secondary demolition. The FC offers unmatched power all the way out to the tip. The FC series utilizes a solid upper with no welds and press-fit pivot group (as with ShearCore mobile shears), which allows for tolerances tight enough to shear rebar all the way out to the tip. Full-length side plates are machined from solid 3” high-yield structural plate steel, resulting in no weld seams.
FS Mobile Shears and FC Demolition shears can be installed on a variety of carriers, fitting everything from smaller excavators up to massive high-reach demo machines. All shears are rated for up to 5,500 psi. The company manufactures approximately 180 shears total, annually and as a division of Exodus Global, is also a privately held, family business. Exodus Global has invested in state-of the-art equipment where product design, engineering and manufacturing are located, at their world-class Wisconsin facility, established in 2014. With customers throughout the world, and an especially strong market presence domestically and in the United Kingdom, Exodus Global includes BladeCore, Connect Work Tools and OilQuick Americas.
“Customer’s processing volume can range from 1,000 to 50,000 tons a month and demand for our products is very high right now. We are committed to never compromising quality and increasing output as much as possible within those boundaries. We simultaneously strive to increase the size of our service and parts teams in order to stay ahead of our customers,” McDevitt said.
Published in the September 2022 Edition of American Recycler News
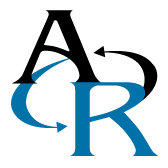