Making shoe soles and washing solvent drenched rags instead of discarding disposables are two ways General Motors (GM) is approaching its goal of becoming a zero waste manufacturer.
With the addition of six landfill free sites in Mexico and England, the company’s landfill free count totals 131 facilities.
Luton Assembly and Ellesmere Port Assembly achieved landfill free status, making all 18 Opel/Vauxhall manufacturing plants in Europe landfill free, which means daily waste is recycled, reused or converted to energy.
The addition of two engine plants, a warehouse, and technical center at GM’s Toluca, Mexico complex mean all of GM de Mexico assembly, engine and transmission plants plus various non-manufacturing operations – a total of 16 facilities – send no waste to landfills.
The Toluca facilities work closely with resource management suppliers to find higher uses for their byproducts, such as turning polystyrene foam packaging into footwear. GM takes the material to a warehouse where it is baled and sent to be crushed and densified into pellets. Those pellets are combined with other polymers to create shoe soles.
Getting all employees in a plant to sort their waste in the appropriate bins can be a challenge. These new landfill-free sites used a variety of tools to educate and inspire, from recycling courses to training videos that help employees understand the environmental benefits and business case. The teams conduct audits to identify improvement opportunities, and recognize employees who drive progress. Some plants designate a green champion in each part of the plant to drive participation.
Since the first GM plant achieved landfill free status 10 years ago, the company has been using evolving and cost effective technology to chip away at tough waste streams. Hiring a waste management company specializing in challenging byproducts versus general waste was key to Ellesmere Port Assembly’s success. The partnership gave the team a better understanding of options for material such as paint residue and sealants used in the car assembly process.
Ellesmere Port is also in a trial project to wash rags used to wipe up solvent instead of using disposable rags, potentially cutting rag waste to zero.
Other new landfill free facilities include the Uzbekistan Engine plant; a Chevrolet sales office in India; an IT Innovation center building (Georgia); a Howell spare parts operation (Michigan); and customer care and aftersales facilities in Cincinnati, Willow Run (Michigan), Rancho Cucamonga (California), Woodstock (Ontario, Canada) and Langley (Vancouver, Canada).
Published in the March 2016 Edition of American Recycler News
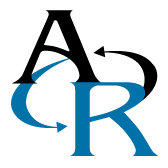