Revolutionary change of body and platform to drastically reduce weight – with that policy, Takayuki Takahashi, assistant chief engineer and the body and exterior project leader, supervised the vehicle body development for the second generation N-BOX by Honda.
“The first thing we did at the start of development was to create the ultimate in light body and chassis from scratch,” said Takahashi. “We ignored both collision safety and maneuvering stability and worked only on creating the ideal lightweight car, then added whatever was missing. We would not have been able to create something bold unless we start from scratch.”
The completed prototype car was not well-balanced but showed a lot of potential. Keeping this ideal form in mind, Takahashi and other design and research team members started developing the body of a car superior in every aspect, from fuel efficiency, acceleration and deceleration, to cornering.
The process for creating the ultimate light body was simple. Honda replaced traditionally used materials with tough and light ones. The frequent use of high tensile steel for the body panels will provide significant weight reduction, thought Takahashi.
“High tensile steel is strong in tension. If we use thinner panels with the same strength as regular ones, then we can reduce the weight by that amount,” he explained.
Steel sheets come in various types depending on tensile strength, from 270 MPa grade to 1,180 MPa grade; high tensile steel are from about 440 MPa grade or higher while ultra-high tensile steels are from 980 MPa grade or higher.
Since the previous N-BOX used high tensile steel 780 MPa grade or higher for around 15 percent of its body, Takahashi planned to raise this rate to nearly half all at once.
However, not all panels can be easily replaced with high tensile steel. It’s strong but hard to bend and easily breaks, which means it’s also difficult to process and limits the places where it can typically be used. Takahashi sought help from the materials research team, saying “To make the car so much lighter, we need to use high tensile steel here and there. We need a strong material that doesn’t break.”
“Of course, I didn’t just thrust this demand on them. The materials research team have been constantly studying materials evolution along with steel manufacturers, and have been testing which materials to make available for use and when. Under these circumstances, I gave my request for the necessary materials,” said Takahashi.
The team wanted to produce a mini vehicle that overturns conventional wisdom. Inspired by the enthusiasm of Takahashi and the design team, the steel manufacturer, pressed steel fabricator, and factory actively collaborated in testing materials with various properties and their processing methods. They were able to use high tensile steel in many parts of the body, including the outer panel of the center pillar between the front and rear doors with 1,180 MPa steel – a world first.
Thus, the use of high tensile steel 780 MPa grade or higher rose to about 47 percent for the second generation N-BOX, which made the dramatic weight reduction possible.
Published in the October 2018 Edition
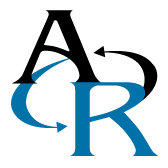